عیوب رایج جوشکاری استیل
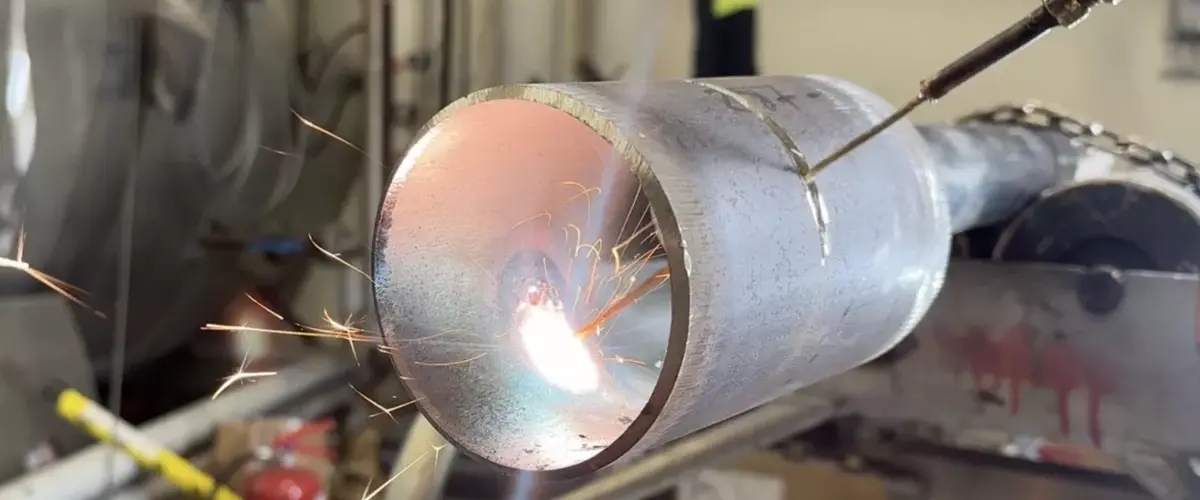
جوشکاری به عنوان یکی از روشهای اصلی اتصال قطعات فلزی، نقش بسیار مهمی در صنایع مختلف ایفا میکند. با این حال، استفاده نادرست از این فرآیند میتواند منجر به ایجاد عیوب مختلفی در جوش شود که در صورت عدم شناسایی و رفع به موقع، میتواند ایمنی و عملکرد سازهها و تجهیزات را به خطر اندازد. عیوب جوشکاری ناشی از عوامل متعددی مانند تنظیمات نادرست دستگاه جوشکاری، آلودگی سطح فلز، نوع الکترود، سرعت جوشکاری و مهارت جوشکار است. در این مقاله، انواع مختلف عیوب جوشکاری، دلایل ایجاد آنها و روشهای پیشگیری و رفع آنها مورد بررسی قرار میگیرد تا با آگاهی از این موارد بتوان از بروز چنین مشکلاتی در فرایند جوشکاری جلوگیری کرده و کیفیت و ایمنی اتصالات جوشکاری را افزایش داد.
ایجاد عیوب در جوشکاری
جوشکاری، به عنوان یکی از پرکاربردترین روشهای اتصال قطعات فلزی، در عین حال میتواند منجر به ایجاد عیوب مختلفی در قطعه کار شود. دلیل اصلی این امر، دماهای بسیار بالای ایجاد شده در ناحیه جوش است که تغییرات متعددی را در ساختار میکروسکوپی و خواص مکانیکی فلز ایجاد میکند. این تغییرات میتوانند منجر به بروز عیوبی مانند ترکها، تخلخلها، ناخالصیها و تغییر شکل در جوش و مناطق مجاور آن شوند. علاوه بر این، تنشهای حرارتی ایجاد شده در حین سرد شدن جوش نیز میتوانند باعث ایجاد ترکهای تنشی و تغییر شکل در قطعه شوند. عیوب جوشکاری نه تنها بر ظاهر و یکپارچگی ظاهری قطعه تأثیر میگذارند، بلکه میتوانند به طور جدی بر استحکام، دوام و قابلیت اطمینان آن نیز تأثیرگذار باشند. به همین دلیل، شناسایی و جلوگیری از بروز این عیوب از اهمیت بسیار بالایی برخوردار است. برخی از عیوب جوشکاری، مانند ترکها، بسیار خطرناک بوده و میتوانند منجر به شکست ناگهانی قطعه شوند. برای تشخیص این نوع عیوب، از روشهای مختلف تستهای غیرمخرب (NDT) استفاده میشود. انتخاب روش مناسب NDT به عوامل مختلفی مانند نوع فلز، هندسه قطعه و نوع جوشکاری بستگی دارد.
لوله اینچ بالا استیل به دلیل استحکام و مقاومت بسیار بالای خود در برابر خوردگی، در صنایع مختلفی مانند نفت و گاز، پتروشیمی، صنایع غذایی، ساختمان و زیرساخت های سنگین مورد استفاده قرار می گیرند. این لوله ها برای انتقال سیالات با فشار بالا، ساخت سازه های بزرگ و مقاوم و همچنین در کاربردهایی که نیاز به مقاومت در برابر حرارت و خوردگی بالا دارند، بسیار مناسب هستند. از جمله ویژگی های بارز لوله های استیل با قطر بالا می توان به مقاومت در برابر سایش، ضربه و فشار، قابلیت جوشکاری و شکل پذیری خوب، طول عمر بالا و ظاهر زیبا اشاره کرد.
برای خرید انواع لوله استیل با کیفیت بالا و قیمت مناسب، همین حالا با کارشناسان بای آهن تماس بگیرید.
دلایل اصلی ایجاد عیوب جوشکاری
جوشکاری، فرآیندی حیاتی در اتصال قطعات فلزی است، اما به دلیل پیچیدگیهای ذاتی آن، امکان بروز عیوب مختلفی در جوش وجود دارد. این عیوب که میتوانند به طور جدی بر استحکام و دوام سازه تأثیر بگذارند، اغلب ناشی از عوامل متعددی هستند.
پارامترهای جوشکاری و تأثیر آنها بر کیفیت جوش:
- سرعت جوشکاری: سرعت زیاد یا کم جوشکاری میتواند منجر به عیوبی مانند نفوذ ناقص، تخلخل یا ترک شود.
- جریان جوشکاری: تنظیم نادرست جریان (کم یا زیاد بودن) میتواند باعث ایجاد عیوبی مانند سوختگی، ذوب ناقص یا تخلخل شود.
- ورودی حرارت: حرارت ورودی بالا میتواند باعث ایجاد تنشهای حرارتی و در نتیجه ترک شود.
- تمیزی سطح: وجود آلودگی روی سطح قطعه کار میتواند منجر به ایجاد عیوبی مانند تخلخل یا عدم ذوب شود.
- روش جوشکاری: انتخاب روش نامناسب جوشکاری برای نوع فلز یا ضخامت قطعه کار میتواند به بروز عیوب مختلفی منجر شود.
عوامل دیگری که میتوانند بر کیفیت جوش تأثیر بگذارند:
- نوع فلز پایه: خواص مکانیکی و شیمیایی فلز پایه بر رفتار آن در حین جوشکاری و احتمال ایجاد عیوب تأثیر میگذارد.
- نوع الکترود یا سیم جوش: انتخاب نامناسب الکترود یا سیم جوش میتواند به ایجاد عیوبی مانند تخلخل یا عدم ذوب منجر شود.
- مهارت جوشکار: مهارت جوشکار در تنظیم پارامترهای جوشکاری و اجرای صحیح روش جوشکاری بسیار مهم است.
- محیط جوشکاری: شرایط محیطی مانند رطوبت، باد و دما میتوانند بر کیفیت جوش تأثیر بگذارند.
رایجترین عیوب جوشکاری استیل و راههای جلوگیری از آنها
جوشکاری استیل به دلیل خواص منحصر به فرد این فلز، نیازمند دقت و توجه بیشتری نسبت به سایر فلزات است. عیوب ایجاد شده در جوشکاری استیل نه تنها ظاهر کار را تحت تاثیر قرار میدهند، بلکه میتوانند به طور جدی بر استحکام و مقاومت خوردگی اتصال تأثیر بگذارند. در این مقاله، به بررسی رایجترین عیوب جوشکاری استیل و دلایل ایجاد آنها میپردازیم.
- ناخالصیها (Inclusions): وجود ناخالصیهای فلزی یا غیرفلزی مانند اکسیدها، سولفورها، ترکیبات تنگستن و مس در ناحیه جوش، میتواند باعث کاهش استحکام و افزایش احتمال ترکخوردگی شود. این مشکل معمولاً به دلیل تمیز نبودن سطح فلز قبل از جوشکاری، استفاده از الکترود نامناسب یا تنظیمات نادرست دستگاه جوشکاری رخ میدهد.
- نفوذ ناقص مذاب: در این عیب، مذاب به طور کامل به عمق شیار جوش نفوذ نمیکند و اتصال کاملی بین دو قطعه ایجاد نمیشود. این مشکل میتواند به دلیل پارامترهای نامناسب جوشکاری، استفاده از الکترود نامناسب یا طراحی نامناسب ناحیه جوش رخ دهد.
- تخلخل (Porosity): حبس گاز در داخل جوش باعث ایجاد حفرههای ریز یا درشت میشود که به تخلخل معروف است. تخلخل میتواند به دلیل رطوبت موجود در الکترود، گاز محافظ نامناسب یا سرعت جوشکاری بالا ایجاد شود.
- بریدگی کنار جوش (Undercut): این عیب به صورت یک شیار در لبه جوش ظاهر میشود و باعث کاهش استحکام و افزایش احتمال ترکخوردگی میشود. بریدگی کنار جوش معمولاً به دلیل جریان جوشکاری بالا، سرعت جوشکاری زیاد یا استفاده از الکترود نامناسب رخ میدهد.
- ترکخوردگی: ترکها یکی از جدیترین عیوب جوشکاری هستند و میتوانند به صورت گرم (در حین جوشکاری) یا سرد (پس از سرد شدن) رخ دهند. دلایل ایجاد ترکها متنوع است و شامل تنشهای حرارتی، ناخالصیها، هیدروژن تردی و طراحی نامناسب اتصال میشود.
- پر نشدن خط جوش (Under-fill): زمانی رخ میدهد که حوضچه جوش به طور کامل ناحیه اتصال را پر نکند و ارتفاع آن کمتر از سطح فلز پایه باشد. این عیب معمولاً به دلیل سرعت جوشکاری بالا، حرارت ورودی کم یا تنظیم نادرست پارامترهای جوشکاری ایجاد میشود. پر نشدن خط جوش میتواند باعث کاهش استحکام اتصال و تمرکز تنش در ناحیه جوش شود.
- ترک (Crack): ترکها یکی از جدیترین عیوب جوشکاری هستند و میتوانند به صورت سرد یا گرم ایجاد شوند. ترکهای سرد معمولاً پس از سرد شدن جوش و به دلیل تنشهای داخلی ایجاد میشوند، در حالی که ترکهای گرم در حین جوشکاری و به دلیل عوامل مختلفی مانند ناخالصیها، هیدروژن تردی و تنشهای حرارتی ایجاد میشوند. ترکها میتوانند به صورت طولی (در امتداد خط جوش) یا عرضی (عمود بر خط جوش) باشند و به طور قابل توجهی استحکام اتصال را کاهش میدهند.
- نفوذ اضافی یا گرده اضافی (Excess reinforcement or penetration): این عیب زمانی رخ میدهد که ارتفاع جوش از حد مجاز بیشتر باشد و باعث ایجاد برآمدگی در سطح جوش شود. نفوذ اضافی میتواند به دلیل سرعت جوشکاری کم، جریان جوشکاری بالا یا زاویه نامناسب الکترود ایجاد شود. این عیب علاوه بر ایجاد ظاهر نامناسب، میتواند باعث تمرکز تنش و کاهش مقاومت خستگی اتصال شود.
- همپوشانی یا اورلپ (Overlap): این عیب زمانی رخ میدهد که فلز جوش روی سطح فلز پایه گسترش یافته و به آن متصل نشده باشد. اورلپ معمولاً به دلیل سرعت جوشکاری کم، زاویه نامناسب الکترود یا تنظیم نادرست پارامترهای جوشکاری ایجاد میشود. اورلپ میتواند باعث کاهش استحکام اتصال و ایجاد تمرکز تنش شود.
راهکارهایی برای بهبود کیفیت اتصالات
همانطور که در بخشهای قبلی به آن پرداختیم، عیوب جوشکاری میتوانند به دلایل مختلفی رخ دهند و کیفیت و عملکرد یک اتصال را به شدت تحت تأثیر قرار دهند. اگرچه پیشگیری از بروز عیوب همواره بهترین راهکار است، اما در برخی موارد ممکن است نیاز به اصلاح یا رفع این عیوب باشد.
روشهای رفع عیوب جوشکاری:
روشهای رفع عیوب جوشکاری بسته به نوع عیب، جنس فلز و اهمیت اتصال متفاوت خواهد بود. برخی از روشهای رایج عبارتند از:
- حذف و جوشکاری مجدد: در بسیاری از موارد، سادهترین و موثرترین راه برای رفع عیوب جوشکاری، حذف قسمت معیوب و جوشکاری مجدد آن است. البته این روش ممکن است در برخی موارد به دلیل هزینه یا زمانبر بودن مقرون به صرفه نباشد.
- عملیات حرارتی: عملیات حرارتی یکی از روشهای رایج برای بهبود خواص مکانیکی و رفع برخی از عیوب جوشکاری مانند تردی و تنشهای داخلی است. به عنوان مثال، برای کاهش تنشهای پسماند و بهبود چقرمگی، میتوان از عملیات حرارتی تنشزدایی استفاده کرد.
- ماشینکاری: در برخی موارد، میتوان با استفاده از روشهای ماشینکاری مانند فرزکاری، تراشکاری یا سنگزنی، قسمتهای معیوب جوش را برداشته و سطح جوش را صاف کرد.
- جوشکاری تعمیری: در مواردی که عیب جوشکاری در یک ناحیه کوچک باشد، میتوان با استفاده از روشهای جوشکاری تعمیری مانند جوشکاری با الکترود تنگستنی (TIG) یا لیزر، عیب را برطرف کرد.
- استفاده از مواد پرکننده: در برخی موارد، میتوان از مواد پرکننده برای پر کردن حفرهها و تخلخلهای موجود در جوش استفاده کرد.
استانداردهای پذیرش عیوب جوش
در دنیای جوشکاری، دستیابی به یک اتصال کاملاً بدون عیب تقریباً غیرممکن است. به همین دلیل، استانداردهای مختلفی برای تعیین حد مجاز انواع مختلف عیوب جوش در کاربردهای مختلف تدوین شده است. این استانداردها با در نظر گرفتن عوامل متعددی مانند نوع فلز، روش جوشکاری، ضخامت قطعه، کاربرد نهایی و شرایط کاری، محدودیتهایی را برای اندازه، تعداد و نوع عیوب مجاز در جوش تعیین میکنند.
لوله های استیل و لوله مسی هر دو در صنایع مختلف کاربرد گسترده ای دارند، اما ویژگی ها و کاربردهای متفاوتی دارند. لوله های استیل به دلیل مقاومت بسیار بالا در برابر خوردگی، حرارت و فشار، در صنایع نفت و گاز، پتروشیمی و صنایع غذایی کاربرد فراوانی دارند. این لوله ها همچنین در ساخت سازه های بزرگ و مقاوم نیز مورد استفاده قرار می گیرند. از سوی دیگر، لوله های مسی به دلیل هدایت حرارتی بالا و انعطاف پذیری، بیشتر در سیستم های گرمایشی و سرمایشی، لوله کشی آب و گاز در ساختمان ها و صنایع غذایی استفاده می شوند. به طور کلی، انتخاب بین لوله استیل و مسی به عوامل مختلفی مانند مقاومت در برابر خوردگی، هدایت حرارتی، هزینه، کاربرد نهایی و شرایط محیطی بستگی دارد.