بررسی لولهها و انواع کاربردی آنها
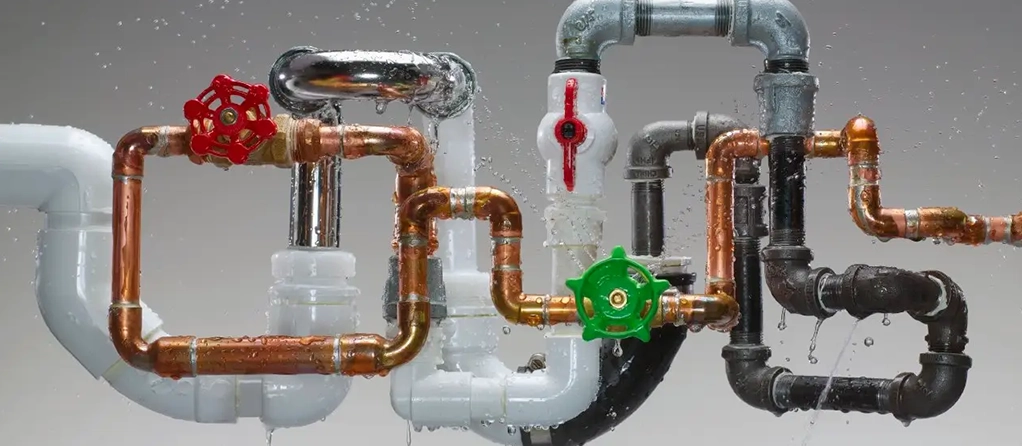
لوله یکی از اجزای کلیدی در انتقال سیالاتی مانند آب، گاز و سایر مایعات است که بهطور معمول به شکل استوانهای توخالی طراحی میشود. هدف اصلی از بهکارگیری لولهها، هدایت منظم و کنترلشده جریان سیال از نقطهای به نقطهی دیگر است. لولهکشی در بخشهای مختلفی از جمله صنایع پالایشگاهی، نیروگاهها، خطوط انتقال آب و فاضلاب، سامانههای گرمایشی و سرمایشی و سایر تأسیسات صنعتی کاربرد فراوان دارد. در ادامه این مطلب، به بررسی کامل کاربردهای مختلف لوله، انواع آن و روند تولید آن خواهیم پرداخت.
آشنایی بیشتر با مشخصات و انتخاب لولهها
لولهها براساس ویژگیهایی نظیر قطر بیرونی، ضخامت دیواره و برخی شاخصهای فنی دیگر دستهبندی میشوند. برای محاسبه قطر داخلی لوله، ابتدا باید قطر خارجی و ضخامت دیواره آن را مشخص کرد.
جنس لولهها بسیار متنوع است و از مواد مختلفی مانند فلزات، آلیاژها، سرامیک، فایبرگلاس، بتن و انواع پلاستیکها ساخته میشوند. انتخاب نوع و جنس لوله باید متناسب با نوع پروژه، شرایط محیطی و ویژگیهای فنی از جمله فشار و دمای مورد نیاز صورت گیرد. عواملی چون هزینه، میزان خوردگی، و نوع سیال نیز در این انتخاب نقش کلیدی دارند.
از نظر طول، لولهها در اندازههای گوناگونی تولید میشوند و بر اساس نیاز پروژه میتوان از لولههای کوتاه یا بلند استفاده کرد. برای انتخاب صحیح لوله در سیستمهای انتقال سیال، نکات زیر باید مورد توجه قرار گیرد:
- دبی و فشار سیال
- نوع سیال و میزان خورندگی آن
- شرایط محیطی و اقلیمی محل نصب
- نوع نصب (روکار یا توکار)
- ارتعاشات احتمالی در سیستم
در زمینه تعیین ضخامت لوله نیز معمولاً از دو استاندارد اصلی استفاده میشود:
- طراحی دقیق بر اساس شرایط عملکردی سیستم: مناسب برای پروژههای حساس و انتقال سیالات گرانقیمت؛ اگرچه اقتصادی نیست.
- استاندارد فلنج: رایجتر و مقرونبهصرفهتر؛ این روش امکان تعمیم کلاسهای لولهکشی در طراحیهای مختلف با متریال مشابه را فراهم میسازد.
سفر در گذر زمان با تاریخچه لولهکشی
از دیرباز، نیاز انسان به آب برای آشامیدن، شستوشو و کشاورزی، او را به سمت طراحی و اجرای روشهایی برای انتقال آب سوق داده است. نخستین نشانههای لولهکشی به تمدن دره سند در هندوس بازمیگردد، جایی که شواهدی از استفاده از لولههای مسی برای انتقال آب کشف شده است.
در ایران نیز آثار ارزشمندی از سیستمهای آبرسانی باستانی بهدست آمده است. یکی از برجستهترین نمونهها، سیستم لولهکشی کشفشده در محوطهی تاریخی «فراش» واقع در ساحل شرقی رودخانه سیمره و در نزدیکی مرز استان لرستان است. این سازهی شگفتانگیز که قدمتی بیش از پنج هزار سال دارد، از لولههای سفالی بههمپیوسته تشکیل شده بود که بهطور محلی تولید و پخته میشدند.
این یافتهها نشاندهنده دانش فنی و مهندسی پیشرفته در زمینه آبرسانی در تمدنهای کهن بوده و جایگاه مهمی را برای تاریخچه لولهکشی در ایران و جهان رقم زدهاند.
منظور از رده لوله چیست؟
منظور از "رده لوله" که اغلب به "اسکجول لوله" (Schedule Number) نیز معروف است، یک شاخص استاندارد برای تعیین ضخامت دیواره لوله نسبت به قطر خارجی آن است. این عدد(مانند Sch 40، Sch 80، Sch 160 ) مستقیماً با توانایی لوله در تحمل فشار داخلی مرتبط است؛ به این صورت که با افزایش عدد اسکجول، ضخامت دیواره لوله برای قطر خارجی ثابت بیشتر شده و در نتیجه مقاومت آن در برابر فشار بالاتر میرود. جدولهای استاندارد مانندASME B36.10M) ) ضخامت دقیق متناظر با هر عدد اسکجول و قطر اسمی لوله (NPS) را مشخص میکنند.
انواع لوله و دستهبندی آنها بر اساس کاربرد و جنس
لولهها به عنوان یکی از حیاتیترین اجزای زیرساختهای صنعتی، شهری و خانگی، نقش کلیدی در انتقال انواع سیالات (مایعات)، گازها و حتی مواد جامد دارند. با توجه به تنوع بیشمار نیازها در دما، فشار، نوع ماده انتقالی (خورندگی، سمی بودن، ویسکوزیته و ...)، محیط نصب (دفنی، روکار، زیر آب)، و ملاحظات اقتصادی، انواع بسیار گوناگونی از لولهها با جنسها، روشهای ساخت و مشخصات فنی متفاوت توسعه یافتهاند. شناخت دستهبندیهای رایج لولهها برای انتخاب گزینه مناسب در هر پروژه ضروری است.
لولهها را میتوان بر اساس معیارهای مختلفی دستهبندی کرد که مهمترین آنها جنس ماده سازنده، روش ساخت، و کاربرد نهایی است. در ادامه به برخی از انواع رایج بر اساس این دستهبندیها میپردازیم:
۱. انواع بر اساس جنس ماده اصلی:
- لولههای فلزی: پرکاربردترین نوع در صنایع سنگین، نفت و گاز، پتروشیمی، نیروگاهها، و خطوط انتقال آب و گاز اصلی.
- لولههای فولادی: این دسته خود تنوع بسیار بالایی دارد و پرمصرفترین نوع لوله در جهان است.
- لولههای فولاد کربنی: برای کاربردهای عمومی در دما و فشار متوسط استفاده میشوند. مانند ASTM A53, A106))
- لولههای فولاد آلیاژی: حاوی عناصری مانند کروم (Cr) و مولیبدن (Mo) برای افزایش مقاومت در برابر دماهای بالا، خزش، و خوردگی. (مانند استاندارد ASTM A335 با گریدهای معروف P11, P22, P5, P9 که قبلاً مورد بحث قرار گرفتند.)
- لولههای فولاد ضد زنگ (استیل): به دلیل مقاومت عالی در برابر خوردگی، زنگزدگی، و همچنین خواص بهداشتی و تحمل دماهای بسیار بالا یا پایین، در صنایع غذایی، دارویی، شیمیایی، و محیطهای دریایی یا خورنده کاربرد فراوان دارند. گریدهای رایج آنها سری ۳۰۰ (مانند ۳۰۴ و ۳۱۶) هستند.
- لولههای چدنی: عمدتاً در سیستمهای فاضلاب ثقلی و خطوط انتقال آب با فشار نسبتاً پایین استفاده میشدند، اما امروزه لولههای فولادی یا پلاستیکی در بسیاری از این کاربردها جایگزین شدهاند. دوام بالا اما شکنندگی از ویژگیهای آنهاست.
- لوله مسی: رایج در سیستمهای لولهکشی آب آشامیدنی داخل ساختمان، سیستمهای گرمایشی و سرمایشی (HVAC)، و خطوط گازهای طبی به دلیل مقاومت در برابر خوردگی، قابلیت شکلپذیری، و خواص آنتیباکتریال طبیعی.
- لولههای فولادی: این دسته خود تنوع بسیار بالایی دارد و پرمصرفترین نوع لوله در جهان است.
- لولههای پلاستیکی: سبک وزن، مقاوم در برابر خوردگی و مواد شیمیایی، سطح داخلی صاف، نصب آسان و هزینه کمتر در برخی کاربردها. تحمل دمایی و فشاری آنها معمولاً کمتر از لولههای فلزی است.
- PVC پلی وینیل کلراید: عمدتاً برای آب سرد، فاضلاب، ناودانی، و داکتهای کابل برق استفاده میشود. ارزان و مقاوم در برابر مواد شیمیایی، اما در برابر حرارت و ضربه محدودیت دارد.
- PE پلی اتیلن: شامل HDPE (پلی اتیلن سنگین) و LDPE (پلی اتیلن سبک). به دلیل انعطافپذیری بالا و مقاومت در برابر خوردگی، برای خطوط انتقال آب، شبکههای توزیع گاز طبیعی (لوله گازی پلی اتیلنی)، فاضلاب، و کاربردهای کشاورزی (آبیاری قطرهای) بسیار مناسباند.
- PP-R پلی پروپیلن رندوم کوپلیمر: که در ایران غالباً با عنوان لولههای سبز شناخته میشوند. برای سیستمهای لولهکشی آب سرد و گرم داخل ساختمان به دلیل تحمل دمای بالاتر نسبت به PVC و خواص بهداشتی استفاده میشوند.
- PEX پلی اتیلن شبکهای: به دلیل انعطافپذیری بسیار بالا، مقاومت دمایی خوب، و نصب سریع، در سیستمهای لولهکشی آب سرد و گرم داخل ساختمان و گرمایش از کف کاربرد دارند.
- لولههای بتنی: در اندازههای بسیار بزرگ برای خطوط انتقال آب و فاضلاب با فشار پایین یا سیستمهای ثقلی (گرانشی) استفاده میشوند. دوام بالایی دارند اما سنگین و شکننده هستند.
- لولههای کامپوزیتی (FRP/GRP): ساخته شده از الیاف تقویتکننده (مانند شیشه) و ماتریس پلیمری (مانند رزینهای اپوکسی یا پلی استر). بسیار مقاوم در برابر خوردگی، سبک وزن، و دارای نسبت استحکام به وزن بالا. برای خطوط انتقال مواد شیمیایی خورنده، آب و فاضلاب در محیطهای صنعتی و دریایی کاربرد دارند.
۲. انواع بر اساس روش ساخت (برای لولههای فلزی):
- لوله بدون درز/ مانیسمان :این لولهها مستقیماً از یک قطعه شمش فلزی بدون هیچگونه درز جوشی تولید میشوند. به دلیل یکنواختی ساختار و مقاومت بالاتر در برابر فشار، برای کاربردهای حساس با فشار و دمای کاری بالا (مانند خطوط انتقال نفت و گاز تحت فشار، بویلرها، مبدلهای حرارتی) ایدهآل هستند. لولههای مانیسمان رده ۴۰ و رده ۸۰ نمونههایی از لولههای بدون درز هستند که رده آنها نشاندهنده ضخامت دیواره است.
- لولههای جوشی: این لولهها از خم کردن ورق فلزی و جوش دادن درز (لوله درزدار) آن تولید میشوند. تولید آنها معمولاً سریعتر و کمهزینهتر است. برای کاربردهای عمومیتر با فشار کاری پایینتر مانند خطوط انتقال آب، سازهها، و برخی خطوط گاز فشار پایین استفاده میشوند. روشهای مختلف جوشکاری (مانند ERW, SAW, EFW ) وجود دارد که بر خواص لوله تأثیر میگذارد.
۳. انواع بر اساس پوشش یا عملیات تکمیلی:
- لوله گالوانیزه: لولههای فولادی (عمدتاً کربنی) که پس از تولید با لایهای از فلز روی (به روش غوطهوری داغ یا الکتروگالوانیزاسیون) پوشانده میشوند. این پوشش مقاومت لوله را در برابر زنگزدگی و خوردگی افزایش میدهد. عمدتاً برای خطوط آب غیر آشامیدنی، حصارکشی، سازههای گلخانهای و برخی کاربردهای عمومی استفاده میشوند. استفاده از آنها برای خطوط لوله گازی طبیعی به دلیل احتمال جدا شدن پوسته روی و آسیب به تجهیزات حساس رایج نیست.
- لولههای با پوشش محافظ: شامل پوششهای داخلی یا خارجی مانند اپوکسی، پلی اتیلن سهلایه (3LPE)، قیر یا سیمان برای محافظت بیشتر در برابر خوردگی در محیطهای خاص (مانند خطوط لوله دفنی یا انتقال فاضلاب خورنده).
انتخاب نوع لوله در نهایت به شرایط خاص هر پروژه وابسته است. درک دقیق ماهیت سیال یا گاز انتقالی، دمای کار، فشار طراحی، محیط نصب، عمر مفید مورد انتظار و بودجه در دسترس، مهندسان را قادر میسازد تا از میان این تنوع گسترده، مناسبترین گزینه را انتخاب کرده و شبکهای ایمن، کارآمد و مقرون به صرفه طراحی و اجرا کنند.
توضیح برخی از انواع خاص لولهها و کاربردهای آنها
در کنار دستهبندیهای کلی لولهها بر اساس جنس (فلزی، پلاستیکی، بتنی) یا روش ساخت (بدون درز، جوشی)، انواع دیگری از لولهها بر اساس ویژگیهای فنی خاص، روش تولید متمایز یا کاربرد غالبشان در بازار شناخته میشوند. شناخت این انواع میتواند در انتخاب دقیقتر لوله برای نیازهای مشخص کمککننده باشد. در ادامه به توضیح برخی از این انواع میپردازیم:
۱. لوله مبلی (لوله سبک / لوله روغنی):
- تعریف و مشخصات: لولههای مبلی که با نامهای "لوله سبک" یا "لوله روغنی" نیز شناخته میشوند، لولههای فولادی درزداری هستند که از ورق فولادی نورد سرد شده (ورق روغنی) با ضخامت نسبتاً کم (معمولاً از ۰.۴ میلیمتر تا ۱.۵ میلیمتر) تولید میشوند. فرآیند نورد سرد باعث میشود سطح این ورقها بسیار صاف و دقیق باشد. این لولهها به دلیل وزن پایین، سطح با کیفیت، دقت ابعادی خوب، جوشپذیری و فرمپذیری عالی، و قابلیت بالای آبکاری (مانند آبکاری کروم یا نیکل برای ظاهر زیبا و مقاومت به خوردگی)، در صنایع مختلفی مورد استفاده قرار میگیرند.
- کاربردها: ساخت انواع مبلمان فلزی (میز، صندلی، تخت)، قطعات داخلی خودرو (مانند اسکلت صندلی)، تولید اگزوز خودرو، ساخت لوازم خانگی (مانند پایههای میز اتو، رختآویز)، دوچرخهسازی، تجهیزات ورزشی و نمایشگاهی، و مصارف دکوراتیو.
۲. لوله جدار چاه:
- تعریف و مشخصات: لوله جدار چاه لولهای است که در هنگام حفر چاههای عمیق (آب، نفت، گاز) درون گمانه چاه قرار داده میشود تا از ریزش دیوارههای ناپایدار چاه جلوگیری کرده و پایداری آن را تضمین کند. جنس این لولهها معمولاً از فولاد یا گاهی پلی اتیلن سنگین (HDPE) است. نوع خاص و بسیار پرکاربرد آن، لوله جدار چاه مشبک یا شیاردار است که دارای سوراخها یا شیارهای مشخصی روی دیواره خود است. این شیارها (که غالباً قوسی شکل هستند) به ورود سیال (آب، نفت) از لایههای زمین به داخل لوله کمک کرده و در عین حال به عنوان فیلتر عمل کرده و از ورود ذرات خاک و سنگ به داخل چاه جلوگیری میکنند، که این امر کیفیت آب خروجی و عمر مفید پمپ را افزایش میدهد.
- کاربردها: تثبیت و مسلح کردن دیواره چاههای آب، نفت و گاز، افزایش بهرهوری و جلوگیری از افت دبی در چاههای آب، استفاده در سیستمهای زهکشی و کنترل سطح آبهای زیرزمینی.
۳. لوله اسپیرال:
- تعریف و مشخصات: لوله اسپیرال نوعی لوله فولادی درزدار است که از نورد کردن ورق یا نوار فولادی به صورت مارپیچی (حلزونی) و سپس جوشکاری درز حاصل شده به روش جوش زیر پودری (SAW) تولید میشود. روش جوشکاری معمولاً دو طرفه (Double Submerged Arc Welding - DSAW) برای اطمینان از استحکام درز است. مزیت اصلی تولید به روش اسپیرال، امکان ساخت لولههایی با قطرهای بسیار بزرگ (که تولید آنها با روشهای دیگر دشوار یا غیرممکن است) با استفاده از ورقهایی با عرض استاندارد است.
- کاربردها: خطوط اصلی انتقال آب در مسافتهای طولانی و پروژههای بزرگ آبی، خطوط انتقال نفت و گاز با قطر بالا، استفاده به عنوان شمعهای فولادی در سازههای عمرانی، و کاربردهای سازهای بزرگ.
۴. لوله صنعتی:
- تعریف و مشخصات: اصطلاح لوله صنعتی بیشتر یک عنوان کلی و رایج در بازار است و معمولاً به لولههای فولادی کربنی (اغلب درزدار / جوشی) با مشخصات متنوع اطلاق میشود که برای مصارف عمومی در صنایع، ساخت و ساز، و سازههای فلزی به کار میروند. این لولهها معمولاً از ورق فولادی نورد گرم (ورق سیاه) یا نورد سرد تولید شده و جوشکاری میشوند. ضخامت و ابعاد آنها متناسب با کاربردهای مختلف صنعتی، ساختمانی یا سازهای متفاوت است. این لولهها بر اساس استانداردهای مختلفی تولید میشوند و برای انتقال سیالات با فشار پایین یا متوسط یا به عنوان عضو سازهای مناسب هستند.
- کاربردها: ساخت انواع سازههای فلزی (مانند خرپاها، قابها، اسکلتهای سبک)، استفاده در ماشینآلات و تجهیزات صنعتی، خطوط انتقال سیالات غیرحساس با فشار پایین یا متوسط (مانند آب غیرشرب، هوای فشرده)، پایهها و ستونهای سبک، و کاربردهای عمومی در کارخانهها و کارگاهها.
۵. لوله داربستی:
- تعریف و مشخصات: لوله داربستی نوع خاصی از لوله فولادی (اغلب کربنی و درزدار) است که به طور انحصاری برای ساخت سازههای موقت داربست در پروژههای ساختمانی، تعمیراتی و صنعتی طراحی و تولید میشود. تفاوت اساسی آن با لولههای انتقال سیال در این است که وظیفه آن تحمل بارهای سازهای و ایجاد تکیهگاه ایمن برای کارگران و مصالح در ارتفاع است و نیازی به تحمل فشار داخلی ندارد. مشخصات فنی لوله داربستی (مانند قطر خارجی استاندارد و حداقل ضخامت دیواره) تابع مقررات ایمنی کار در ارتفاع و استانداردهای مربوط به داربست است. این لولهها معمولاً با رنگ یا پوشش گالوانیزه برای محافظت در برابر زنگزدگی عرضه میشوند.
- کاربردها: تنها و اصلیترین کاربرد آن، ساخت سازههای موقت داربست جهت دسترسی ایمن به نمای ساختمانها و سازهها، نگهداری موقت بخشهایی از سازه در حین ساخت یا تعمیر، و ایجاد سکوهای کاری در ارتفاع است.
۶. لوله مسی:
- تعریف و مشخصات: لوله مسی لولهای است که به طور کامل از فلز مس خالص یا آلیاژهای مس با خلوص بالا تولید میشود. مس فلزی با رسانایی حرارتی و الکتریکی بسیار بالا، مقاومت طبیعی در برابر خوردگی توسط آب، و قابلیت شکلپذیری و خمکاری عالی است. لولههای مسی معمولاً به روش بدون درز تولید شده و در انواع سخت، نیمهسخت و نرم موجود هستند که انعطافپذیری آنها را تعیین میکند. (برخلاف متن قبلی، لوله مسی به هیچ عنوان زیرمجموعه لوله استیل نیست؛ این دو از نظر ترکیب شیمیایی و خواص کاملاً متفاوتند).
- کاربردها: لولهکشی آب آشامیدنی سرد و گرم در ساختمانهای مسکونی و تجاری، خطوط انتقال گازهای طبی در بیمارستانها، خطوط مبرد (گاز فریون) در سیستمهای تهویه مطبوع و تبرید (HVAC) به دلیل انتقال حرارت عالی، سیستمهای آبپاش اطفاء حریق، و در برخی کاربردهای صنعتی خاص.
مهمترین کاربرد انواع لوله در صنایع، ساختمان و زیرساختها
لولهها به عنوان یکی از حیاتیترین اجزای زیرساختهای صنعتی، ساختمانها، و شبکههای شهری، نقش بنیادین در توسعه و عملکرد این حوزهها ایفا میکنند. وظیفه اصلی آنها انتقال ایمن و کارآمد انواع سیالات (اعم از آب، نفت، مواد شیمیایی)، گازها (مانند گاز طبیعی)، بخار، و گاهی مواد جامد (نظیر پودرها یا دوغابها) از نقطهای به نقطه دیگر است. تنوع بینظیر نیازها در هر کاربرد خاص، از نظر دما، فشار، ماهیت ماده انتقالی، شرایط محیطی، و ملاحظات اقتصادی، منجر به توسعه و استفاده از انواع گوناگون لولهها با جنسها، روشهای ساخت و مشخصات فنی کاملاً متفاوت شده است. درک این تنوع و ارتباط آن با نیازهای هر حوزه، کلید انتخاب بهینه و موفقیت در طراحی و اجرای سیستمهای لولهکشی است. در ادامه به مهمترین حوزههای کاربرد انواع لولهها در صنعت، ساختمان و زیرساختها اشاره میکنیم:
۱. انتقال آب و فاضلاب:
این حوزه شامل طیف وسیعی از کاربردها، از شبکههای پیچیده آبرسانی شهری برای تأمین آب شرب سالم، خطوط انتقال آب خام از سدها یا چاهها به تصفیهخانهها، شبکههای گسترده جمعآوری و انتقال فاضلابهای بهداشتی و صنعتی، تا سیستمهای زهکشی و جمعآوری آبهای سطحی و باران است. نیازهای این بخش شامل مقاومت در برابر خوردگی (چه از سمت داخل لوله و چه از سمت محیط اطراف)، عدم نفوذپذیری، دوام بلندمدت، و در مورد آب شرب، حفظ کیفیت بهداشتی آب است.
- انواع لولههای رایج: لولههای فولادی (با پوششهای داخلی و خارجی مناسب برای جلوگیری از خوردگی)، لولههای پلی اتیلن (PE) که به دلیل مقاومت عالی در برابر خوردگی و انعطافپذیری بالا در شبکههای آبرسانی و فاضلاب مدرن بسیار پرکاربردند، لولههای PVC که عمدتاً برای خطوط فاضلاب و ناودانی و گاهی آب سرد فشار پایین استفاده میشوند، لولههای بتنی (برای خطوط اصلی با قطر بزرگ و فشار پایین یا ثقلی)، لولههای چدنی (که در سیستمهای قدیمیتر آبرسانی و فاضلاب کاربرد داشتند و هنوز در برخی موارد خاص استفاده میشوند)، و لولههای کامپوزیتی (FRP/GRP) برای انتقال فاضلابهای صنعتی یا آبهای بسیار خورنده.
۲. انتقال انرژی (نفت، گاز، بخار و سیالات داغ):
این کاربرد یکی از حیاتیترین و سختگیرانهترین حوزهها برای لولههاست و شامل خطوط لوله عظیم انتقال نفت خام و فرآوردههای نفتی در مسافتهای طولانی، شبکههای فشار قوی و فشار ضعیف توزیع گاز طبیعی، خطوط بخار با فشار و دمای بسیار بالا در نیروگاههای تولید برق و واحدهای صنعتی، و خطوط انتقال سیالات با دمای بالا در فرآیندهای گوناگون است. در این کاربردها، مقاومت در برابر فشار داخلی بالا، تحمل دماهای عملیاتی (بالا یا پایین)، مقاومت در برابر خوردگی (به ویژه در حضور ترکیبات خورنده در سیال)، و اطمینان از آببندی کامل برای جلوگیری از نشتی مواد خطرناک حیاتی است.
- انواع لولههای رایج: لولههای فولادی نقش اصلی را در این بخش ایفا میکنند، به ویژه لولههای بدون درز (مانیسمان) و لولههای جوشی با کیفیت بسیار بالا (مانند اسپیرال یا جوش مستقیم) که بر اساس استانداردهای سختگیرانهای نظیر API 5L تولید میشوند. برای انتقال بخار با فشار و دمای بسیار بالا یا سیالات داغ خورنده در صنایع نفت، گاز و پتروشیمی، از لولههای فولادی آلیاژی دما بالا تحت استاندارد ASTM A335 با گریدهای مختلف (مانند لوله P11, لوله P22, لوله P5, لوله P9) استفاده میشود که مقاومت فوقالعادهای در برابر خزش و اکسیداسیون در دماهای بالا دارند. در شبکههای توزیع گاز شهری با فشار پایین یا متوسط نیز لولههای پلی اتیلن (PE) به دلیل مزایایی مانند انعطافپذیری، مقاومت به خوردگی و نصب آسان، کاربرد وسیعی یافتهاند.
۳. خطوط فرآیندی و انتقال مواد در صنایع مختلف:
این بخش شامل شبکههای لولهکشی گسترده در داخل کارخانجات صنایع شیمیایی، پتروشیمی، دارویی، غذایی، فولاد، سیمان و غیره است. در این فرآیندها، لولهها ممکن است برای انتقال مواد شیمیایی خورنده (اسیدها، بازها، حلالها)، سیالات با ویسکوزیته بالا، دوغابهای ساینده، بخار، یا سیالاتی که نیاز به بالاترین سطح بهداشت دارند، استفاده شوند. تنوع مواد انتقالی و شرایط عملیاتی در این بخش بسیار زیاد است.
- انواع لولههای رایج: لولههای فولاد ضد زنگ (استیل) به دلیل مقاومت عالی در برابر خوردگی و خواص بهداشتی در صنایع شیمیایی، دارویی و غذایی بسیار پرکاربردند. لولههای فولادی آلیاژی برای شرایط دما و فشار بالا یا محیطهای خاص، لولههای پلاستیکی مهندسی خاص (مانند PVDF, CPVC, PTFE) برای مقاومت در برابر مواد شیمیایی بسیار خورنده، لولههای کامپوزیتی (FRP/GRP) و در برخی موارد، لولههای فلزی با پوششهای داخلی مقاوم به مواد شیمیایی استفاده میشوند.
۴. کاربردهای سازهای و پشتیبانی:
در این کاربرد، لولهها به عنوان عضو سازهای و باربر به کار میروند و نه برای انتقال سیال. استحکام مکانیکی، مقاومت در برابر بارهای وارده (کششی، فشاری، خمشی)، و دوام در برابر عوامل محیطی در این بخش اهمیت دارد.
- انواع لولههای رایج: لوله داربستی که به طور خاص برای ساخت سازههای موقت داربست طراحی شده است، لولههای فولادی (عمدتاً جوشی) با مقاطع گرد یا مربعی در ساخت اسکلتهای فلزی سبک، خرپاها، پایهها و ستونها، و به عنوان شمعهای فولادی در پروژههای عمرانی، و لولههای فولادی یا پلاستیکی به عنوان کاندوئیت (محافظ) برای عبور کابلهای برق.
۵. سیستمهای تهویه مطبوع (HVAC) و آتشنشانی:
این بخش شامل لولهکشی برای انتقال آب سرد یا گرم در سیستمهای گرمایش و سرمایش ساختمانها، و لولهکشی تحت فشار برای انتقال آب یا کف در سیستمهای اطفاء حریق است.
- انواع لولههای رایج: لولههای فولادی (به ویژه برای خطوط آب آتشنشانی که نیاز به تحمل فشار دارند)، لولههای مسی برای خطوط مبرد در سیستمهای تهویه مطبوع (به دلیل انتقال حرارت عالی و مقاومت در برابر فشارهای بالا) و همچنین برای خطوط آب در برخی ساختمانها، و لولههای پلاستیکی خاص (مانند PEX یا PP-R) در سیستمهای گرمایش از کف و لولهکشی آب سرد و گرم داخل ساختمان.
روشهای اصلی تولید لوله: بدون درز و درزدار
تولید لولههای فلزی به روشهای مختلفی صورت میگیرد که هر یک بر ساختار داخلی، خواص مکانیکی و در نهایت کاربردهای لوله تأثیر چشمگیری دارند. به طور کلی، لولههای فلزی بر اساس نحوه شکلدهی ورق یا شمش و اتصال لبهها به دو دسته اصلی تقسیم میشوند: لولههای بدون درز و لولههای درزدار. این تفاوت در فرآیند تولید، مهمترین عامل در تفاوت قابلیتهای آنها، به ویژه در مواجهه با فشارهای داخلی و خارجی بالا، دماهای عملیاتی حساس و محیطهای خورنده است.
۱. فرآیند تولید لولههای بدون درز / مانیسمان:
این روش تولید، همانطور که از نامش پیداست، منجر به تولید لولههایی بدون هیچگونه خط جوش یا درز در طول آنها میشود. فرآیند تولید لولههای بدون درز با استفاده از شمشهای فولادی توپر و گرم آغاز میشود. شمش پس از حرارت دیدن تا رسیدن به دمای مناسب برای شکلدهی، وارد مرحله اصلی میشود که در آن یک سنبه یا مندریل (Mandrel) در مرکز شمش چرخانده شده و همزمان فشار از بیرون توسط غلتکها وارد میشود. این فرآیند که به سوراخکاری (Piercing) معروف است، مرکز شمش توپر را خالی کرده و آن را به یک لوله اولیه ضخیم و کوتاه (بلوم توخالی) تبدیل میکند. در مراحل بعدی، این بلوم توخالی با استفاده از نورد کششی و غلتکهای دقیق، به طول و ضخامت دیواره مورد نظر کشیده و شکل داده میشود. لولههای بدون درز به دلیل ساختار یکپارچه و همگن، استحکام مکانیکی بسیار بالایی در برابر فشارهای داخلی دارند و برای کاربردهایی که نیاز به تحمل فشار بالا، دماهای شدید (بسیار بالا یا پایین)، یا مقاومت در برابر خزش دارند، ایدهآل هستند (مانند خطوط انتقال نفت و گاز تحت فشار بالا، بویلرها، مبدلهای حرارتی و لولهکشی در صنایع پتروشیمی). لولههای تولید شده با این روش در ایران غالباً با نام مانیسمان شناخته میشوند.
۲. فرآیند تولید لولههای درزدار (Welded Pipes):
تولید لولههای درزدار با استفاده از ورق یا نوار فولادی (کویل) صورت میپذیرد. در این روش، ورق فولادی پس از برش به عرض مناسب، از میان مجموعهای از غلتکها عبور داده میشود تا به تدریج به شکل یک استوانه باز (با دو لبه در امتداد یکدیگر) درآید. سپس، این دو لبه در طول لوله به روشهای مختلف جوشکاری به یکدیگر متصل میشوند. روشهای رایج جوشکاری عبارتند از:
- جوش مقاومتی الکتریکی (ERW - Electric Resistance Welding): در این روش، حرارت لازم برای جوشکاری از طریق عبور جریان الکتریکی با فرکانس بالا از لبههای در تماس ورق ایجاد میشود. فشار همزمان باعث اتصال دو لبه میشود. این روش عمدتاً برای تولید لولههای با قطر کوچک و متوسط استفاده میشود.
- جوش زیر پودری (SAW - Submerged Arc Welding): در این روش، جوشکاری توسط یک یا چند الکترود در زیر لایهای از فلاکس گرانولی انجام میشود. این روش برای تولید لولههای با قطر بزرگتر به کار میرود. لولههای SAW میتوانند به صورت درز مستقیم (LSAW - Longitudinal SAW، از جوش دادن درز طولی یک ورق) یا به صورت درز مارپیچی/حلزونی (اسپیرال - HSAW / SSAW - Helical/Spiral SAW، از نورد کردن ورق یا نوار به صورت مارپیچ و جوشکاری درز حلزونی) تولید شوند.
پس از جوشکاری، درز جوش ممکن است برادهبرداری و پرداخت شود و سپس لوله تحت عملیات حرارتی و تستهای لازم قرار میگیرد. لولههای درزدار به دلیل سرعت تولید بالاتر و استفاده از ورق، معمولاً از نظر اقتصادی مقرون به صرفهتر هستند و برای طیف وسیعی از کاربردها با فشار کاری پایین تا متوسط (مانند خطوط انتقال آب، برخی خطوط گاز فشار پایین، سازههای فلزی و داربست) مناسب هستند.
تفاوت بین لوله (Pipe) و تیوب(Tube)
اگرچه در محاوره روزمره یا حتی گاهی در برخی صنایع، واژگان "لوله" و "تیوب" ممکن است به جای یکدیگر استفاده شوند، اما در استانداردها و مهندسی، این دو دارای تفاوتهای مشخصی هستند:
- لوله (Pipe): در درجه اول برای انتقال سیالات و گازها طراحی شده است. اندازه آن بر اساس قطر اسمی لوله (NPS - Nominal Pipe Size) و رده یا اسکجول (Schedule Number) (که ضخامت دیواره را نسبت به قطر خارجی استاندارد تعیین میکند) مشخص میشود. قطر خارجی واقعی برای یک NPS مشخص در اندازههای کوچک متغیر است، اما از NPS 14 به بالا، قطر خارجی تقریباً برابر با عدد NPS است. تمرکز در لولهها بیشتر بر قابلیت حجم عبوری و تحمل فشار است.
- تیوب (Tube): یک اصطلاح کلیتر است و اغلب برای کاربردهای سازهای، مکانیکی، مبدلهای حرارتی، بویلرها، یا ابزار دقیق استفاده میشود. اندازهگذاری تیوبها معمولاً بر اساس قطر خارجی دقیق (Outside Diameter - OD) و ضخامت دیواره (Wall Thickness) با تلرانسهای بسیار دقیقتر از لولهها انجام میشود. شکل مقطع تیوب میتواند دایرهای، مربعی، مستطیلی یا اشکال دیگر باشد.