سوالات پرتکرار در حوزه پایپینگ
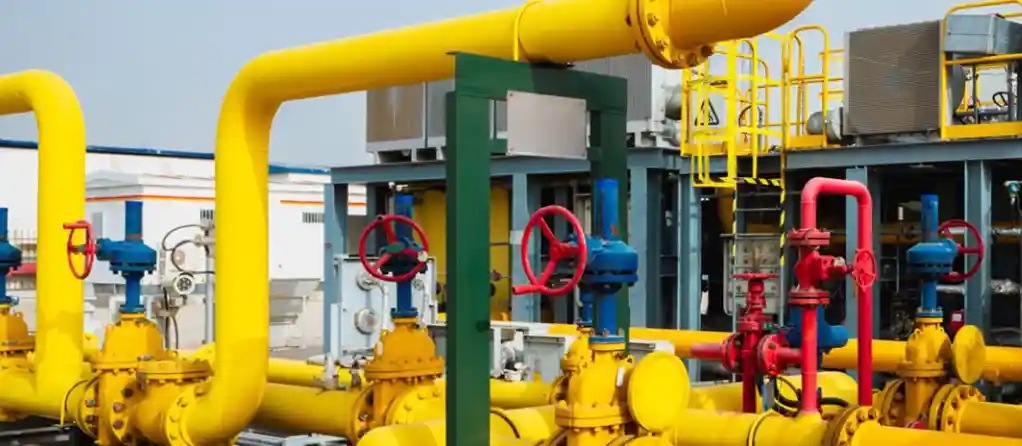
سیستمهای لولهکشی صنعتی یا پایپینگ، شریانهای حیاتی هر واحد تولیدی و صنعتی هستند که جریان جابهجایی انواع مواد اولیه، سیالات فرآیندی، و محصولات نهایی را در داخل و خارج از کارخانه امکانپذیر میسازند. درک صحیح اصول پایپینگ و رفع ابهامات رایج در این حوزه، نقش کلیدی در بهینهسازی فرآیندها، افزایش ایمنی و ارتقاء کیفیت انتقال مواد دارد.
در این بخش، با پرداختن به سوالات متداول شما در زمینه پایپینگ، بای آهن بر روشن کردن جنبههای کلیدی سیستمهای لولهکشی صنعتی و ارائه راهکارهای مؤثر برای بهینهسازی مسیر فراوری و تضمین کیفیت انتقال مواد در واحدهای مختلف تمرکز دارد.
استانداردهای کلیدی در طراحی، ساخت و نصب سیستمهای پایپینگ
طراحی، ساخت، نصب، تست و بهرهبرداری از سیستمهای لولهکشی صنعتی (پایپینگ)، فرآیندهایی بسیار تخصصی هستند که برای تضمین ایمنی، قابلیت اطمینان، دوام و عملکرد صحیح در شرایط مختلف عملیاتی (فشار، دما، نوع سیال)، نیازمند رعایت دقیق مجموعهای از استانداردها، کدها و مشخصات فنی هستند. این استانداردها توسط سازمانهای معتبر ملی و بینالمللی توسعه یافته و راهنمای مهندسان، سازندگان و بازرسان در تمام مراحل یک پروژه پایپینگ هستند. آشنایی با این استانداردها برای هر فرد فعال در این حوزه ضروری است. مهمترین سازمانها و استانداردهای مرتبط با پایپینگ که عموماً مهندسی پایپینگ به آنها تکیه میکند، عبارتند از:
- انجمن مهندسان مکانیک آمریکا (ASME - American Society of Mechanical Engineers):
ASME یکی از تأثیرگذارترین سازمانها در زمینه تدوین استانداردها و کدهای مهندسی در جهان است و به خصوص در حوزه مخازن تحت فشار و پایپینگ، استانداردهای آن به طور گستردهای مورد پذیرش قرار گرفتهاند. اصلیترین استانداردهای ASME در حوزه پایپینگ، کدهای ASME B31 هستند که کدهای طراحی اصلی برای انواع مختلف سیستمهای لولهکشی تحت فشار را شامل میشوند. هر زیرمجموعه B31 به کاربرد خاصی اختصاص دارد، مانند:
- ASME B31.1 : استاندارد لولهکشی نیروگاهی (برای نیروگاههای تولید برق، بویلرها، و سیستمهای مرتبط)
- ASME B31.3: استاندارد لولهکشی فرآیندی (پرکاربردترین کد در صنایع شیمیایی، پتروشیمی، پالایشگاه، داروسازی و غیره- قیمت لوله نفت)
- ASME B31.4: استاندارد سیستمهای لولهکشی انتقال مایعات هیدروکربنی و مایعات دیگر (مانند خطوط لوله نفت و فرآوردهها)
- ASME B31.8: استاندارد سیستمهای لولهکشی انتقال و توزیع گاز (برای خطوط لوله گاز طبیعی- قیمت لوله گازی)
علاوه بر کدهای طراحی B31، ASME استانداردهای مهمی در زمینه ابعاد، جنس و مشخصات فنی اتصالات لوله (مانند فلنجها، فیتینگها، شیرآلات) تحت سری ASME B16 و همچنین استاندارد ASME Section IX برای تعیین صلاحیت جوشکاران و رویههای جوشکاری (که برای تضمین کیفیت جوش اتصالات لوله حیاتی است) ارائه میدهد.
- مؤسسه نفت آمریکا (API- American Petroleum Institute):
API استانداردهایی را عمدتاً برای صنایع نفت، گاز و پتروشیمی تدوین و منتشر میکند. استانداردهای API نقش مهمی در مشخصات مواد، تجهیزات و فرآیندهای مرتبط با این صنایع دارند. در حوزه پایپینگ، استاندارد API 5L که مشخصات فنی لولههای فولادی خطی (Line Pipe) مورد استفاده در انتقال نفت و گاز در مسافتهای طولانی را تعیین میکند، یکی از شناخته شدهترین و پرکاربردترین استانداردهای جهانی است. API همچنین استانداردهای دیگری برای شیرآلات، فلنجها و سایر اجزای مورد استفاده در خطوط لوله نفت و گاز دارد.
- انجمن آمریکایی تست و مواد (ASTM - American Society for Testing and Materials):
ASTMیکی از بزرگترین سازمانهای استاندارد بینالمللی است که هزاران استاندارد توافقی را برای مواد، محصولات، سیستمها و خدمات مختلف تدوین و منتشر میکند. در حوزه پایپینگ، استانداردهای ASTM نقش حیاتی در تعریف مشخصات فنی مواد پایه ایفا میکنند. این استانداردها ترکیب شیمیایی، خواص مکانیکی (مانند استحکام کششی، تسلیم، سختی)، عملیات حرارتی، و الزامات تست برای مواد مختلفی که در ساخت لولهها، فیتینگها، فلنجها، پیچ و مهرهها، واشرها و سایر اجزای سیستم لولهکشی استفاده میشوند (مانند فولاد کربنی، فولاد آلیاژی، فولاد ضد زنگ، مواد پلاستیکی و غیره) را مشخص مینمایند. به عنوان مثال، استاندارد ASTM A106 (برای لولههای فولادی کربنی بدون درز برای سرویس در دمای بالا)، ASTM A335 (برای لوله آلیاژی بدون درز برای سرویس در دمای بالا - شامل گریدهای P5, P9, P11, P22)، ASTM A53 (برای لولههای فولادی جوشی و لوله بدون درز با کاربرد عمومی)، و ASTM A312 (برای لولههای فولاد ضد زنگ بدون درز و جوشی) نمونههایی از استانداردهای پرکاربرد ASTM در حوزه مواد پایپینگ هستند.
- انجمن جوش آمریکا(AWS - American Welding Society):
AWS اصلیترین سازمان در ایالات متحده است که بر توسعه استانداردها و دستورالعملهای مربوط به فرآیندهای جوشکاری، صلاحیت جوشکاران، و بازرسی جوش تمرکز دارد. از آنجایی که جوشکاری یکی از روشهای اصلی اتصال لولهها، فیتینگها و فلنجها در بسیاری از سیستمهای پایپینگ صنعتی است، استانداردهای AWS (مانند AWS D1.1 برای جوشکاری سازههای فولادی یا استانداردهای خاصتر برای جوشکاری لوله) نقش بسیار مهمی در اطمینان از کیفیت، استحکام و ایمنی اتصالات جوشی لوله ایفا میکنند. این استانداردها اغلب مکمل الزامات جوشکاری در کدهای طراحی ASME B31 و استاندارد ASME Section IX هستند.
- مؤسسه ملی استاندارد آمریکا (ANSI- American National Standards Institute):
ANSI خود مستقیماً تدوینکننده استانداردهای فنی طراحی پایپینگ نیست، اما نقش مهمی در سیستم استانداردسازی ایالات متحده ایفا میکند. ANSI به عنوان یک نهاد نظارتی و تأییدکننده، استانداردهای توسعه یافته توسط سازمانهای دیگر (مانند ASME، ASTM، API، AWS) را به عنوان استانداردهای ملی آمریکا (ANSI Standards) تأیید و منتشر میکند. بسیاری از استانداردهای پرکاربرد در پایپینگ با پیشوند ANSI نیز شناخته میشوند (مانند ANSI/ASME B31.3). ANSI همچنین نماینده ایالات متحده در سازمانهای استانداردسازی بینالمللی مانند ISO است.
کُدها، استانداردها و دستورالعملها: چارچوب ایمنی و کیفیت در پایپینگ
در دنیای پیچیده مهندسی و صنایع، به ویژه در حوزههای حساسی نظیر لولهکشی تحت فشار (پایپینگ) در پالایشگاهها، نیروگاهها و کارخانجات شیمیایی، تضمین ایمنی عمومی، حفاظت از محیط زیست و اطمینان از عملکرد قابل اعتماد سیستمها، از اهمیت بالایی برخوردار است. برای دستیابی به این اهداف، مجموعهای از قوانین، مقررات، و دستورالعملهای فنی مدون توسط سازمانهای تخصصی و با بهرهگیری از دانش و تجربه متخصصان توسعه یافتهاند که تحت عناوین کُدها (Codes)، استانداردها (Standards) و دستورالعملهای اجرایی (Practices) شناخته میشوند. این اسناد، چارچوب لازم برای طراحی، ساخت، نصب، تست و بازرسی سیستمهای پایپینگ را فراهم میکنند.
استانداردها (Standards):
استانداردها اسناد فنی هستند که توسط انجمنهای مهندسی، سازمانهای استاندارد ملی یا بینالمللی (مانند ASTM, API, ISO) و با فرآیندهای اجماع متخصصان آن حوزه تدوین میشوند. این اسناد مشخصات فنی، الزامات، روشهای آزمون، ابعاد، ویژگیهای عملکردی، یا دستورالعملهای لازم برای مواد، محصولات، فرآیندها یا خدمات را تعیین میکنند. هدف اصلی استانداردسازی، ایجاد یکنواختی در محصولات و خدمات، تضمین کیفیت پایه، قابلیت تبادل بین قطعات سازندگان مختلف، و مستندسازی بهترین شیوهها و دانش فنی موجود است. به عنوان مثال، استاندارد ASTM A106 مشخصات فنی لوله فولادی کربنی بدون درز را تعیین میکند و استاندارد ASME B16.5 ابعاد و متریال استاندارد برای فلنجها را مشخص مینماید. رعایت استانداردها در ذات خود داوطلبانه است، مگر اینکه در یک قرارداد تجاری بین خریدار و فروشنده، یا مهمتر از آن، در یک کُد طراحی یا مقررات قانونی به آنها ارجاع داده شده و اجرایشان اجباری شود.
کُدها (Codes):
کُدها مجموعهای جامع از قواعد و الزامات هستند که حداقل معیارهای ایمنی لازم برای طراحی، ساخت، نصب، تست، بازرسی و گاهی نگهداری انواع خاصی از سیستمها را تعیین میکنند. کُدها معمولاً توسط سازمانهای بزرگ مهندسی (مانند سری کدهای ASME B31 برای لولهکشی تحت فشار) تدوین میشوند و تمرکز اصلی آنها بر تضمین سطح قابل قبولی از ایمنی عمومی و جلوگیری از خطرات احتمالی است. تفاوت کلیدی کُدها با استانداردها در این است که کُدها به گونهای نوشته میشوند که قابلیت پذیرش و تصویب توسط نهادهای نظارتی و دولتی (مانند وزارتخانهها یا سازمانهای آتشنشانی) را داشته باشند و در صورت پذیرش و تبدیل شدن به قانون، اجرای آنها برای کلیه پروژههایی که تحت آن حوزه قضایی قرار دارند، اجباری و لازمالاجرا میگردد. کُدها اغلب برای تعیین الزامات فنی خود، به استانداردهای مختلفی ارجاع میدهند (به عنوان مثال، کد ASME B31.3 ممکن است برای مشخصات فنی لوله به استاندارد لوله چینی A106 و برای ابعاد فلنج به استاندارد ASME B16.5 ارجاع دهد). در واقع، کُدها الزامات اجباری را تعیین میکنند و استانداردها جزئیات فنی لازم برای برآورده کردن آن الزامات را مشخص مینمایند.
دستورالعملهای اجرایی توصیه شده (Recommended Practices):
این اسناد که گاهی توسط سازمانهایی مانند API یا انجمنهای صنعتی دیگر منتشر میشوند، راهنماییها، روشهای پیشنهادی، یا توصیههایی را ارائه میدهند که بر اساس تجربیات موفق، بهترین شیوههای مهندسی یا دانش فنی روز در یک حوزه خاص تدوین شدهاند. این دستورالعملها معمولاً انعطافپذیری بیشتری نسبت به کدها و استانداردها دارند و اجرای آنها عموماً کاملاً داوطلبانه است، مگر اینکه به طور خاص در یک قرارداد یا مشخصات پروژه به آنها اشاره و اجرایشان الزامی شود. هدف آنها ارتقاء سطح عملکرد، کارایی یا ایمنی فراتر از حداقل الزامات کدها و استانداردها است و به عنوان راهنمایی برای بهبود مستمر در صنعت عمل میکنند.
ملاحظات کلیدی در طراحی سیستمهای لولهکشی صنعتی (پایپینگ)
طراحی یک سیستم لولهکشی صنعتی فرآیندی مهندسی است که فراتر از صرف کشیدن خطوط و اتصال تجهیزات است. یک طراحی اصولی باید تضمینکننده ایمنی، قابلیت اطمینان، کارایی عملیاتی، سهولت نگهداری، و توجیه اقتصادی سیستم در طول عمر مفید آن باشد. مهندسان پایپینگ هنگام برنامهریزی و طراحی سیستمهای لولهکشی باید مجموعهای از عوامل کلیدی را به دقت بررسی و لحاظ کنند. نادیده گرفتن هر یک از این عوامل میتواند منجر به مشکلات جدی در فازهای ساخت، نصب، راهاندازی یا بهرهبرداری شود. مهمترین ملاحظات در طراحی پایپینگ عبارتند از:
۱. شرایط عملیاتی و طراحی (دما و فشار):
مهمترین عوامل در تعیین الزامات مقاومت مکانیکی یک سیستم لولهکشی، شرایط دما و فشار سیالی است که قرار است منتقل شود. دما و فشار عملیاتی نرمال، حداکثر دما و فشار ممکن (مانند شرایط اضطراری یا نوسانات فرآیندی)، و حداقل دمای محیطی که سیستم در معرض آن قرار میگیرد (به ویژه برای جلوگیری از پدیده شکنندگی سرد در مواد)، باید به دقت مشخص شوند. این شرایط، مبنای انتخاب جنس لوله، ضخامت دیواره، نوع اتصالات (فلنجی، جوشی، رزوه ای)، و کلاس فشاری شیرآلات و فیتینگها هستند. دماهای بالا میتواند استحکام مواد را کاهش داده و منجر به پدیده خزش (تغییر شکل تدریجی تحت تنش در طول زمان) شود، در حالی که دماهای پایین میتواند انعطافپذیری ماده را کاهش داده و خطر شکست ترد را افزایش دهد. کدهای طراحی پایپینگ (مانند سری ASME B31) دستورالعملهای دقیقی برای انتخاب مواد و تعیین ضخامت دیواره بر اساس دما و فشار طراحی ارائه میدهند.
۲. خواص سیال یا ماده انتقالی:
ماهیت مادهای که قرار است از درون لولهها عبور کند، تأثیر مستقیمی بر انتخاب جنس لوله و طراحی سیستم دارد. خواص سیال مانند:
- خورندگی: آیا سیال اسیدی، قلیایی، حاوی کلراید، گوگرد، یا سایر مواد شیمیایی خورنده است؟ این عامل تعیین میکند که آیا نیاز به استفاده از فولاد ضد زنگ (استیل)، لولههای آلیاژی خاص، لولههای پلاستیکی مقاوم به مواد شیمیایی، یا لولههای با پوشش داخلی مقاوم به خوردگی هست یا خیر.
- فرسایشزایی (Erosivity): آیا سیال حاوی ذرات جامد معلق با سرعت بالا است که میتواند باعث سایش دیواره داخلی لوله شود؟ در این صورت ممکن است نیاز به مواد سختتر، افزایش ضخامت دیواره، یا تغییر در مسیردهی برای کاهش سرعت در زانوها و نقاط تغییر جهت باشد.
- ویسکوزیته و چگالی: این خواص بر افت فشار در طول لوله و در نتیجه بر انتخاب قطر لوله و طراحی سیستم پمپاژ تأثیر میگذارند.
- سمی بودن، اشتعالپذیری یا انفجاری بودن: این عوامل ملاحظات ایمنی بسیار سختگیرانهای را برای طراحی اتصالات، شیرآلات، ابزار دقیق، و سیستمهای تشخیص نشتی تحمیل میکنند و استفاده از مواد با بالاترین سطح اطمینان و جوشکاری با کیفیت بسیار بالا را ضروری میسازند.
۳. شرایط محیطی و خارجی:
محیطی که سیستم لولهکشی در آن نصب میشود نیز باید در نظر گرفته شود. این شامل دمای محیط، رطوبت، اتمسفر خورنده (مانند محیطهای صنعتی آلوده یا نزدیک به دریا)، قرار گرفتن در معرض نور خورشید (که میتواند برخی پلاستیکها را تخریب کند)، خطر یخزدگی سیال در لوله، بارهای ناشی از باد، بارهای زلزلهای، و احتمال آسیب فیزیکی ناشی از فعالیتهای انسانی یا ماشینآلات است. این عوامل بر نیاز به عایقکاری (حرارتی یا محافظت در برابر یخزدگی)، نوع پوشش خارجی لولهها (مانند گالوانیزه یا پوششهای پلیمری سنگین برای لولههای دفنی)، و طراحی و فواصل ساپورتهای لوله برای تحمل بارهای محیطی اثرگذارند.
۴. عمر مفید طراحی شده و قابلیت اطمینان سیستم:
طول عمر مورد انتظار از سیستم لولهکشی، عامل مهمی در انتخاب مواد و سطح کیفیت ساخت است. پروژههای زیرساختی یا صنعتی با عمر مفید طولانی (مثلاً ۳۰ سال یا بیشتر) نیازمند موادی با دوام بسیار بالا، مقاومت عالی در برابر خزش و خستگی (Fatigue) و حداقل نیاز به تعمیرات در طول زمان هستند، حتی اگر هزینه اولیه بالاتری داشته باشند. طراحی باید به گونهای باشد که قابلیت اطمینان سیستم در طول دوره بهرهبرداری تضمین شود، که این امر گاهی مستلزم در نظر گرفتن فاکتورهای ایمنی بالاتر یا حتی طراحی مسیرهای جایگزین (Bypass) برای امکان تعمیر بدون توقف کامل فرآیند است.
۵. قابلیت ساخت، نصب، بهرهبرداری و نگهداری (Constructability, Installability, Operability & Maintainability):
طراحی خوب پایپینگ باید تمام مراحل چرخه حیات پروژه را در نظر بگیرد. طراحی باید به گونهای باشد که ساخت قطعات در کارگاه، حمل و نصب آنها در محل پروژه، دسترسی اپراتورها به شیرآلات، ابزار دقیق و نقاط نمونهبرداری، امکان بازرسیهای دورهای (به عنوان مثال، تستهای غیرمخرب جوشها)، سهولت انجام تعمیرات احتمالی، و همچنین امکان تخلیه (Drain) و هواگیری (Vent) سیستم برای راهاندازی یا تعمیرات، همگی به آسانی و با ایمنی بالا انجام شوند. طراحی مناسب ساپورتها و دسترسی به آنها برای تنظیمات یا بازرسی نیز بخشی از این ملاحظات است.
۶. چیدمان، مسیردهی و ساپورتگذاری (Layout, Routing & Support Engineering):
این جنبه از طراحی، به چگونگی قرارگیری فیزیکی لولهها، تجهیزات، شیرآلات و ابزار دقیق در فضای موجود مربوط میشود. نمودارهای فرآیندی و ابزاردقیق (P&ID) و نقشههای چیدمان کلی (Plot Plans) مبنای اولیه هستند. مسیردهی لولهها باید با حداقل طول ممکن (برای کاهش افت فشار و هزینه)، با پرهیز از موانع فیزیکی و تداخل با سایر تأسیسات (مانند کابلهای برق یا کانالهای هوا)، در نظر گرفتن فضای کافی برای نصب و نگهداری، و با لحاظ کردن نیاز به انعطافپذیری برای جذب تنشهای ناشی از انبساط و انقباض حرارتی صورت گیرد. طراحی دقیق ساپورتها برای تحمل وزن لوله و سیال، بارهای ناشی از باد یا زلزله، و کنترل حرکت و تنش در لوله، حیاتی است. استفاده از نرمافزارهای مدلسازی سهبعدی (3D Modeling) در این مرحله به بهینهسازی چیدمان و جلوگیری از تداخلها کمک شایانی میکند.
۷. هزینههای سرمایهای و عملیاتی (Initial & Lifecycle Costs):
ملاحظات اقتصادی بخش جداییناپذیر از فرآیند طراحی هستند. هزینه سیستم لولهکشی میتواند درصد قابل توجهی (گاه تا یک سوم) از کل سرمایهگذاری یک واحد صنعتی را شامل شود. طراح باید به دنبال تعادلی مناسب میان هزینه اولیه (شامل هزینه مواد، ساخت در کارگاه، حمل و نصب در محل) و هزینههای چرخه عمر سیستم باشد. هزینههای چرخه عمر شامل هزینههای انرژی (ناشی از افت فشار)، نگهداری دورهای، تعمیرات، و در نهایت جایگزینی سیستم است. انتخاب مواد با کیفیت بالاتر یا استفاده از روشهای ساخت پیشرفتهتر ممکن است هزینه اولیه بیشتری داشته باشد، اما میتواند با کاهش هزینههای نگهداری، افزایش عمر مفید، و کاهش اتلاف انرژی، در بلندمدت اقتصادیتر باشد. بودجه پروژه و محدودیتهای زمانبندی نیز بر تصمیمات طراحی تأثیر میگذارند.