پیشگیری از خوردگی لولهها
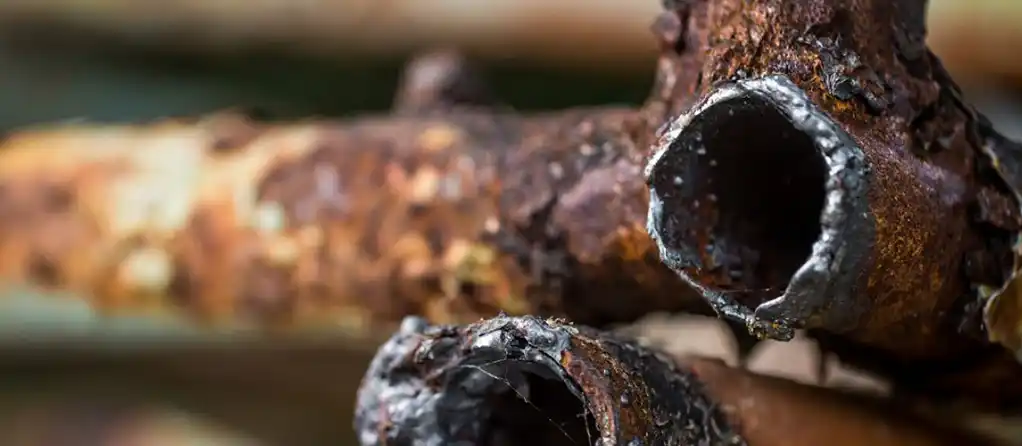
لولههای فولادی به طور گسترده برای انتقال سیالات مانند گاز، نفت و مشتقات آن به کار میروند. بسته به نوع کاربری و شرایط محیطی، این لولهها با ترکیبات شیمیایی و ساختارهای مختلفی تولید میشوند تا بهترین عملکرد را داشته باشند. یکی از چالشهای مهم در استفاده از این لولهها، خوردگی است؛ مشکلی که میتواند به طور مستقیم بر طول عمر و کارایی لولهها تأثیر بگذارد و در نهایت باعث بروز خسارات و اختلال در عملکرد سیستم شود.
چالش خوردگی در لولههای فولادی و پیامدهای آن
استفاده از لولههای فولادی به دلیل مقاومت بالا در برابر فشار و حرارت، همواره یکی از انتخابهای اصلی مهندسین و طراحان در صنایع گوناگون بوده است. این لولهها بهویژه در صنایع حساس و گرانقیمت مانند نفت، گاز، پتروشیمی و نیروگاهها کاربرد گستردهای دارند. اما یکی از مشکلات رایج و جدی در این حوزه، پدیده خوردگی است که میتواند عمر مفید لولهها را بهشدت کاهش داده و عملکرد سیستم را مختل کند.
در سالهای اخیر تلاش شده است تا با ارتقاء کیفیت مواد اولیه و فرآیند تولید، میزان مقاومت لولهها در برابر خوردگی افزایش یابد. با این حال، خوردگی همچنان تهدیدی جدی محسوب میشود که در صورت بیتوجهی، خسارات فنی و اقتصادی قابل توجهی را به دنبال خواهد داشت.
اثرات منفی خوردگی لولههای فولادی شامل:
- کاهش ضخامت دیواره لوله و افت توان تحمل فشار
- افزایش فشار کاری پمپها و کاهش بازدهی جریان
- جدا شدن و حرکت قطعات زنگزده در مسیر سیال
- نیاز به عملیات جوشکاری تخصصی برای ترمیم نقاط آسیبدیده
- افزایش چشمگیر هزینههای تعمیر و نگهداری
با توجه به این چالشها، پیشگیری از خوردگی به یک ضرورت حیاتی در طراحی و بهرهبرداری از خطوط لوله تبدیل شده است. یکی از راهکارهای اصلی، استفاده از پوششهای محافظ مقاوم و استاندارد است. هرچند این اقدام ممکن است هزینه اولیه لولهها را افزایش دهد، اما در بلندمدت با کاهش نیاز به تعمیرات و افزایش طول عمر تجهیزات، کاملاً بهصرفه خواهد بود.
لوله P22 یکی از انواع لوله آلیاژی پرکاربرد در صنایع نفت، گاز، پتروشیمی و نیروگاههاست که به دلیل ترکیب عناصر کروم و مولیبدن، مقاومت بالایی در برابر حرارت و فشار دارد. این نوع لوله برای استفاده در شرایط کاری سخت و دماهای بالا بسیار مناسب است و استانداردهای بینالمللی از جمله ASTM A335 را پوشش میدهد. اگر قصد خرید لوله P22 با کیفیت تضمینشده و قیمت رقابتی را دارید، فروشگاه اینترنتی بای آهن یکی از معتبرترین مراجع تأمین این محصول است. در بای آهن میتوانید با مشاوره تخصصی، ضمانت اصالت کالا و ارسال سریع، تجربهای مطمئن از خرید صنعتی داشته باشید.
عوامل اصلی بروز خوردگی در لولههای فولادی
خوردگی به تغییرات ظاهری و ساختاری لولههای فولادی در اثر عوامل محیطی و شیمیایی گفته میشود که منجر به کاهش دوام و عملکرد آنها میگردد. برای مقابله مؤثر با این پدیده، درک درست از علتهای ایجاد خوردگی و شناخت نوع آن، از اهمیت بالایی برخوردار است.
یکی از مهمترین دلایل خوردگی در لولههای فولادی، رطوبت محیط است. حضور شبنم، بارندگی یا رطوبت بالای هوا میتواند بهراحتی زمینهساز اکسید شدن و پوسیدگی سطح لولهها شود. به همین دلیل، در مناطقی با اقلیم خشک مانند کویرها، لولههای فولادی عمر بیشتری دارند؛ در حالی که مناطق مرطوب، بهویژه شمال کشور، بیشترین میزان خوردگی را تجربه میکنند. برای مقابله با این شرایط، تولیدکنندگان از پوششهای محافظ مقاوم در برابر رطوبت استفاده میکنند.
عامل دیگر، خوردگی میکروبی است؛ نوعی از آسیب که ناشی از فعالیت میکروارگانیسمها در داخل یا خارج لولههاست و میتواند به تخریب ساختاری جدی منجر شود.
به طور کلی، خوردگی لولههای فولادی میتواند در شکلهای مختلفی ظاهر شود:
- خوردگی داخلی
- خوردگی بیرونی
- خوردگی حفرهای
- خوردگی شیاری
شناسایی دقیق نوع خوردگی، پیشزمینهای حیاتی برای انتخاب روش مقابله مناسب و اجرای پوششهای مؤثر است. این موضوع، نقش کلیدی در افزایش عمر مفید و کاهش هزینههای نگهداری سیستمهای لولهکشی ایفا میکند.
روشهای پیشگیری از خوردگی لولههای فولادی
خوردگی لولههای فولادی میتواند خسارتهای جدی به سیستمهای انتقال وارد کند و باعث کاهش طول عمر، افت عملکرد و افزایش هزینههای نگهداری شود. از آنجایی که بسیاری از لولهها در زیر خاک یا محیطهای مرطوب نصب میشوند، استفاده از شیوههای مؤثر محافظتی امری ضروری است. در ادامه، با مهمترین روشهای مقابله با خوردگی آشنا میشوید:
۱. پوشش پلیاتیلن
یکی از قدیمیترین روشهای محافظت از لولهها، استفاده از پوشش پلیاتیلن است. این پوشش مانند یک لایهی عایق عمل کرده و مانع تماس مستقیم لوله با رطوبت میشود. هرچند با گذشت زمان احتمال جدا شدن این پوشش از سطح لوله وجود دارد، اما در بسیاری از موارد هنوز کاربرد دارد.
۲. پوشش اپوکسی
پوشش اپوکسی به دلیل مقاومت بالا در برابر مواد شیمیایی و رطوبت، در صنایع بهویژه خطوط لوله صنعتی بسیار کاربرد دارد. این پوشش بهوسیله غلطک یا اسپری بر روی لوله اعمال میشود و لایهای مقاوم ایجاد میکند.
۳. پوشش آلکیدی
نوع دیگری از پوشش با اجرای مشابه اپوکسی، اما با دوام و مقاومت پایینتر. این روش حدود ۳ تا ۵ سال محافظت مؤثر فراهم میآورد و برای کاربردهای سبکتر مناسب است.
۴. ثابتسازی لولهها
ضربه، ارتعاش و سایش میتوانند سرعت خوردگی را افزایش دهند. استفاده از بستهای U شکل و مهارهای مکانیکی کمک میکند تا لولهها در جای خود محکم مانده و کمتر دچار خوردگی شوند.
۵. رنگهای ضد زنگ
در لولههایی که در زیر زمین قرار میگیرند، رنگهای ضد زنگ نقش مؤثری در محافظت دارند. این رنگها مانع تماس رطوبت با سطح فلز میشوند.
۶. تمیز نگه داشتن لولهها
برای جلوگیری از خوردگی میکروبی، باید لولهها را از آلودگیهای قارچی و باکتریایی دور نگه داشت. نظافت منظم یکی از راهکارهای ساده اما مؤثر است.
۷. کنترل رطوبت و آب
جلوگیری از تماس مداوم لوله با آب یا تنظیم دمای مناسب سیال درون لوله میتواند میزان خوردگی را کاهش دهد. بهویژه، آب گرم خورندگی بیشتری نسبت به آب سرد دارد. برای دیدن انواع لوله آب، روی لینک کلیک کنید.
۸. پوشش پلیاورتان
این نوع پوشش با دوام بالا، تا بیش از ۱۰ سال لولهها را از آسیب محافظت میکند. پلیاورتان در برابر سایش و پوسیدگی بسیار مقاوم است و در کاهش هزینههای بلندمدت نقش مهمی دارد.
۹. جلوگیری از تماس فلز با فلز
تماس فلزات ناهمجنس ممکن است منجر به خوردگی گالوانیکی شود. استفاده از عایق، پد ضد سایش یا حفاظت کاتدی میتواند از این نوع خوردگی جلوگیری کند.
۱۰. استفاده از فلز قربانی (آند فداشونده)
با نصب فلزاتی مانند منیزیم یا روی در کنار لولههای فولادی، میتوان خوردگی را به سمت فلز قربانی هدایت کرد و از آسیب به لوله جلوگیری نمود.
۱۱. پوششدهی کامل لوله و اتصالات
برای محافظت کامل، تمام اجزای سیستم شامل لولهها، اتصالات، پیچها و مهرهها باید پوششدهی یا گالوانیزه شوند تا نقاط ضعف احتمالی حذف گردند.
در نهایت، انتخاب روش مناسب محافظتی بستگی به شرایط محیطی، نوع سیال، نوع لوله (لوله درزدار یا لوله بدون درز) و طول عمر مورد انتظار دارد. سرمایهگذاری در روشهای پیشگیرانه، هزینههای تعمیرات و تعویض را به شکل چشمگیری کاهش میدهد.