کاربرد لولههای مارپیچی
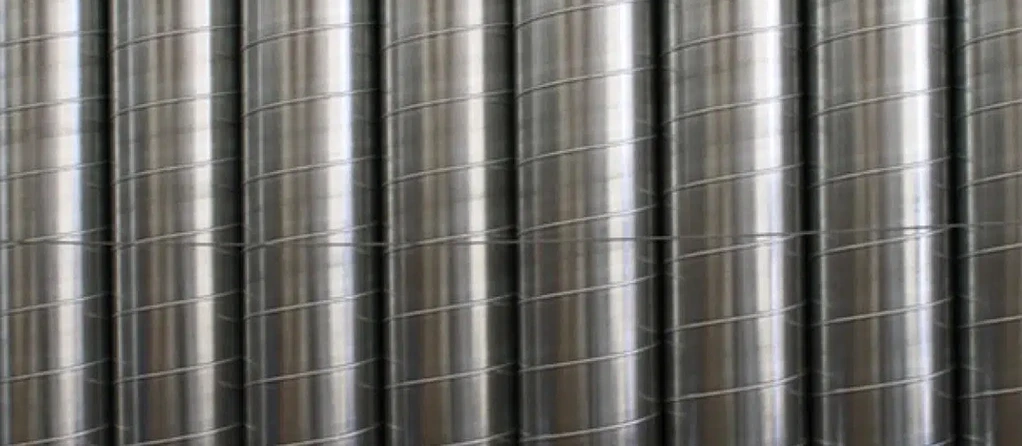
لوله اسپیرال از طریق نورد ورقهای فولادی و جوشکاری آنها به صورت مارپیچی تولید میشوند. این فرآیند منجر به ایجاد لولههایی با طول زیاد، استحکام بالا و سطح داخلی صاف و یکدست میشود. وجود یک درز جوش در سطح خارجی لوله، نه تنها از استحکام آن نمیکاهد، بلکه به دلیل توزیع یکنواخت تنشها، مقاومت آن را در برابر فشار افزایش میدهد.
یکی از مهمترین مزایای لولههای اسپیرال، کاهش اصطکاک سیال در حین جریان است که به معنای کاهش افت فشار و افزایش راندمان سیستم انتقال سیال میباشد. همچنین، امکان تولید این لولهها در قطرها و ضخامتهای مختلف، آنها را برای طیف گستردهای از کاربردها مناسب کرده است.
لولههای اسپیرال به طور گستردهای در صنایع نفت و گاز، پتروشیمی، آب و فاضلاب و صنایع ساختمانی مورد استفاده قرار میگیرند. از جمله کاربردهای مهم این لولهها میتوان به موارد زیر اشاره کرد:
- خطوط لوله انتقال نفت و گاز: به دلیل مقاومت بالا در برابر فشار و خوردگی
- سیستمهای آبرسانی: به دلیل سطح داخلی صاف و کاهش رسوبگذاری
- صنایع پتروشیمی: برای انتقال مواد شیمیایی با دما و فشار بالا
- ساختمانسازی: در ساخت اسکلت فلزی ساختمانها و سازههای صنعتی
در برخی موارد، لولههای اسپیرال میتوانند جایگزین مناسبی برای لولههای استیل باشند، زیرا علاوه بر قیمت مناسبتر، مقاومت خوبی در برابر خوردگی نیز از خود نشان میدهند.
تولید لولههای اسپیرال
تولید لولههای اسپیرال، فرآیندی پیچیده و مهندسی شده است که طی آن ورقهای فولادی به صورت مارپیچی به هم جوش داده میشوند تا لولههایی با قطر و ضخامتهای مختلف تولید شود. این فرآیند به کمک تجهیزات تخصصی و با رعایت استانداردهای دقیق انجام میشود.
- آمادهسازی مواد اولیه: اولین گام در تولید لولههای اسپیرال، آمادهسازی دقیق ورقهای فولادی است. ورقهای فولادی با کیفیت بالا و ابعاد مشخص، بر اساس استانداردهای مربوطه انتخاب میشوند. کیفیت ورقها به طور مستقیم بر روی استحکام و دوام لولههای تولیدی تأثیرگذار است.
- فرآیند نورد: پس از آمادهسازی ورقها، نوبت به فرآیند نورد میرسد. در این مرحله، ورقهای فولادی به صورت مارپیچی به دور یک محور مرکزی پیچیده شده و تحت فشار و حرارت قرار میگیرند. این فرآیند باعث شکلگیری استوانهای میشود که در نهایت به لوله تبدیل خواهد شد. دقت در تنظیم پارامترهای نورد مانند سرعت، فشار و حرارت، از اهمیت بالایی برخوردار است تا از تولید لولههایی با هندسه دقیق و یکنواخت اطمینان حاصل شود.
- جوشکاری دقیق: جوشکاری، مهمترین مرحله در تولید لولههای اسپیرال است. در این مرحله، لبههای ورق فولادی به صورت پیوسته و با استفاده از روشهای جوشکاری پیشرفته مانند جوشکاری زیرپودری به هم متصل میشوند. این روش جوشکاری به دلیل نفوذ عمیق جوش و کیفیت بالا، برای تولید لولههای با استحکام بالا بسیار مناسب است. پارامترهای جوشکاری مانند نوع الکترود، جریان جوشکاری و سرعت آن به دقت تنظیم میشوند تا از کیفیت جوش و یکپارچگی لوله اطمینان حاصل شود.
- عملیات حرارتی (در صورت نیاز): بسته به نوع فولاد و کاربرد نهایی لوله، ممکن است عملیات حرارتی بر روی لولههای تولید شده انجام شود. عملیات حرارتی به منظور بهبود خواص مکانیکی لولهها مانند استحکام، چقرمگی و مقاومت در برابر خوردگی انجام میشود.
- آزمونها و بازرسیهای نهایی: در آخرین مرحله، لولههای تولید شده تحت آزمونهای دقیق و کنترل کیفی قرار میگیرند. آزمونهایی مانند آزمون فشار هیدرواستاتیک، آزمون رادیوگرافی، آزمون اولتراسونیک و آزمونهای متالوگرافی برای ارزیابی کیفیت جوش، وجود عیوب داخلی و انطباق لولهها با استانداردهای مشخص انجام میشود. پس از تأیید کیفیت لولهها، آنها آماده بستهبندی و ارسال به مشتریان میشوند.
تولید لولههای اسپیرال فرآیندی پیچیده و دقیق است که نیازمند تجهیزات پیشرفته و نیروی کار ماهر میباشد. رعایت استانداردهای بینالمللی و کنترل کیفیت در هر مرحله از تولید، تضمینکننده تولید لولههایی با کیفیت بالا و مطمئن است.
انواع لولههای اسپیرال و کاربردهای آنها
لولههای اسپیرال بر اساس جنس مواد اولیه و روش تولید به انواع مختلفی تقسیمبندی میشوند که هر کدام کاربردهای خاص خود را دارند. رایجترین نوع لولههای اسپیرال، لولههای فولادی هستند که از ورقهای فولادی با گریدهای مختلف تولید میشوند. این لولهها به دلیل استحکام بالا، مقاومت در برابر فشار و دما، در صنایع نفت و گاز، پتروشیمی و نیروگاهها کاربرد فراوانی دارند. برای افزایش مقاومت در برابر خوردگی، سطح داخلی و خارجی برخی از لولههای اسپیرال با لایه نازکی از روی پوشش داده میشود که به آنها لولههای اسپیرال گالوانیزه گفته میشود. این نوع لولهها در صنایع آب و فاضلاب و سیستمهای گرمایشی بسیار کاربرد دارند. علاوه بر این، لولههای اسپیرال آلیاژی نیز وجود دارند که از آلیاژهای مختلفی مانند استیل ضدزنگ، نیکل و مس تولید میشوند. این لولهها به دلیل مقاومت بالا در برابر خوردگی و حرارت، در صنایع شیمیایی، دارویی و غذایی کاربرد گستردهای دارند.
انتخاب نوع لوله های اسپیرال
انتخاب نوع لوله اسپیرال به عوامل مختلفی از جمله جنس سیال منتقل شونده، دما و فشار محیط، میزان خوردگی، بودجه و استانداردهای مورد نیاز بستگی دارد. لولههای فولادی کربنی برای انتقال سیالات با فشار بالا مناسب هستند، در حالی که لولههای گالوانیزه برای سیالاتی که احتمال خوردگی دارند، انتخاب بهتری هستند. لوله آلیاژی نیز برای کاربردهای خاص مانند صنایع شیمیایی و دارویی که نیاز به مقاومت در برابر مواد خورنده و حرارت بالا دارند، استفاده میشوند.
مزایای منحصربهفرد لولههای اسپیرال
لولههای اسپیرال به دلیل روش تولید خاص و ویژگیهای منحصر به فرد خود، در صنایع مختلف از محبوبیت بالایی برخوردار هستند. این لولهها به دلیل مقاومت مکانیکی بالا، قابلیت اطمینان و اقتصادی بودن، انتخابی ایدهآل برای بسیاری از پروژهها هستند. برخی از مهمترین مزایای لولههای اسپیرال عبارتند از:
- استحکام و دوام بالا: روش تولید مارپیچی و جوشکاری مستحکم، به این لولهها استحکام و مقاومت بالایی در برابر فشار، ضربه و خوردگی میبخشد.
- انعطافپذیری در طراحی: امکان تولید لولههای اسپیرال در ابعاد و ضخامتهای مختلف و با استفاده از مواد اولیه متنوع، آنها را برای کاربردهای گوناگون مناسب میسازد.
- هزینه مناسب: فرآیند تولید ساده و بهینهسازی شده، هزینه تولید لولههای اسپیرال را نسبت به برخی دیگر از انواع لولهها کاهش میدهد.
- سرعت بالای تولید: امکان تولید سریع این لولهها، آنها را برای پروژههایی با زمانبندی تنگ مناسب میسازد.
- کاهش افت فشار: سطح داخلی صاف و یکنواخت این لولهها، باعث کاهش اصطکاک سیال و در نتیجه کاهش افت فشار میشود.
- نصب آسان: وزن کمتر و انعطافپذیری این لولهها، نصب و راهاندازی آنها را آسانتر میکند.
- طول عمر بالا: با توجه به کیفیت مواد اولیه و فرآیند تولید، لولههای اسپیرال دارای طول عمر بالایی هستند.
معایب و محدودیتهای لولههای اسپیرال
با وجود تمام مزایای لولههای اسپیرال، این نوع لولهها نیز مانند سایر محصولات صنعتی، دارای برخی محدودیتها و معایبی هستند. یکی از مهمترین چالشها در تولید لولههای اسپیرال، کنترل تنشهای پسماند ناشی از فرآیند جوشکاری است. این تنشها میتوانند در درازمدت باعث ایجاد ترک در محل جوش و کاهش مقاومت لوله شوند. همچنین، در برخی موارد، به دلیل پیچیدگی فرآیند تولید، ممکن است عیوبی مانند بیضی شدن سطح مقطع داخلی لوله ایجاد شود که بر عملکرد آن تأثیر میگذارد. علاوه بر این، در صورتی که لولههای اسپیرال با پوشش محافظتی مناسب پوشش داده نشوند، در معرض خوردگی قرار میگیرند.
مقایسه هزینه و پیچیدگی تولید
یکی دیگر از نکات قابل توجه در مورد لولههای اسپیرال، هزینه تولید بالاتر آنها نسبت به برخی انواع دیگر لوله است. فرآیند تولید پیچیدهتر و نیاز به تجهیزات تخصصی، باعث افزایش هزینههای تولید میشود. همچنین، امکان ایجاد عیوب در فرآیند تولید و نیاز به کنترل کیفیت دقیقتر، هزینههای تولید را افزایش میدهد. با این حال، با توجه به مزایای متعدد لولههای اسپیرال، از جمله مقاومت بالا، طول عمر زیاد و قابلیت اطمینان، هزینه بالاتر آنها قابل توجیه است.
کاربرد گسترده لولههای اسپیرال در صنایع مختلف
لولههای اسپیرال به دلیل ویژگیهای منحصر به فردی مانند استحکام بالا، مقاومت در برابر خوردگی و هزینه مناسب، در طیف وسیعی از صنایع مورد استفاده قرار میگیرند. این لولهها در صنایع نفت و گاز برای انتقال سیالات با فشار بالا و دماهای مختلف به کار میروند. همچنین، در صنایع آب و فاضلاب، ساختمانسازی، نیروگاهها و صنایع شیمیایی کاربرد گستردهای دارند. به دلیل سطح داخلی صاف و یکنواخت، این لولهها باعث کاهش اصطکاک سیال و افزایش راندمان سیستمهای انتقال سیالات میشوند.
انتخاب لولههای اسپیرال به عنوان جایگزینی مناسب
لولههای اسپیرال به عنوان جایگزینی مناسب برای لولههای مانیسمان و سایر انواع لولهها در بسیاری از کاربردها مورد توجه قرار گرفتهاند. این لولهها به دلیل انعطافپذیری در تولید، امکان ساخت لولههایی با ابعاد و مشخصات فنی متنوع را فراهم میکنند. همچنین، هزینه تولید پایینتر و سرعت بالای تولید این لولهها، آنها را به گزینه اقتصادی و مناسبی برای بسیاری از پروژهها تبدیل کرده است. با توجه به مزایای ذکر شده، لولههای اسپیرال به یکی از پرکاربردترین انواع لولهها در صنایع مختلف تبدیل شدهاند.