لولهی صنعتی،تنوع و کاربری(بخش دوم)
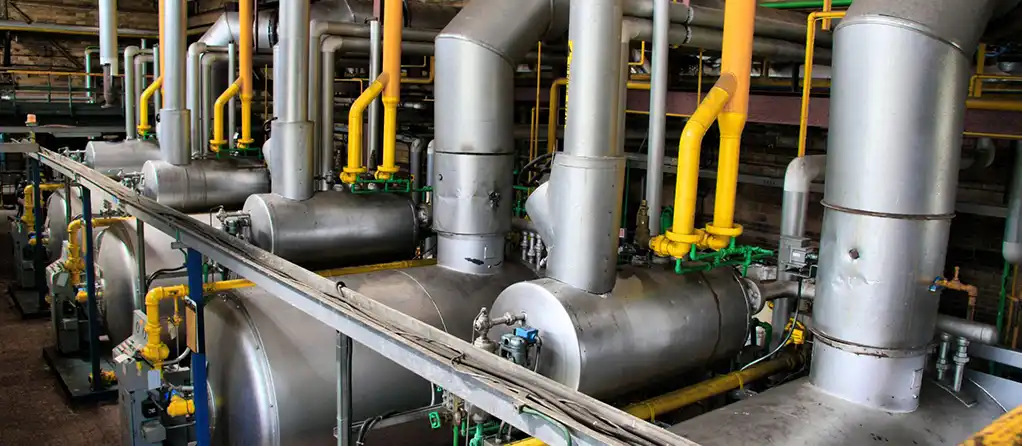
فرآیند تولید لولههای صنعتی
تولید لوله صنعتی، فرایندی دقیق و چند مرحلهای است که با توجه به نوع لوله و استانداردهای مورد نظر، ممکن است متفاوت باشد. به طور کلی، مراحل تولید لولههای صنعتی را میتوان به شرح زیر خلاصه کرد:
- انتخاب مواد اولیه:
انتخاب مواد اولیه نخستین و یکی از مهمترین مراحل تولید لولههای صنعتی است. نوع ماده اولیه بهکاررفته در ساخت لوله، به طور مستقیم بر خواص فیزیکی، شیمیایی و مکانیکی محصول نهایی تاثیر میگذارد و تعیینکننده کاربرد آن در صنایع مختلف خواهد بود. این انتخاب بر اساس فاکتورهایی همچون مقاومت مورد نیاز در برابر خوردگی، فشار کاری، دمای محیط کاربری، نوع سیالی که قرار است در لوله جریان یابد و همچنین هزینه تمام شده محصول انجام میشود. به عنوان مثال، برای انتقال سیالات خورنده از لولههای استیل ضد زنگ استفاده میشود، در حالی که برای انتقال آب در سیستمهای آبرسانی شهری، ممکن است از لولههای پلی اتیلن استفاده شود. بنابراین، در این مرحله، انتخاب مواد اولیه با دقت و بر اساس نیازهای خاص هر پروژه صورت میگیرد تا بهترین عملکرد و طول عمر را برای لوله تضمین کند.
- آمادهسازی مواد:
مرحله آمادهسازی مواد در تولید لولههای صنعتی، گامی حیاتی است که در آن مواد اولیه با توجه به مشخصات فنی مورد نظر برای محصول نهایی، انتخاب و آمادهسازی میشوند. این مرحله شامل انتخاب دقیق نوع ماده اولیه، برش و آمادهسازی اولیه آن برای مراحل بعدی تولید است. انتخاب مواد اولیه بر اساس عواملی همچون مقاومت مورد نیاز در برابر خوردگی، فشار کاری، دمای محیط کاربری، نوع سیالی که قرار است در لوله جریان یابد و همچنین استانداردهای کیفی مشخص میشود. مواد اولیه معمولاً شامل فلزات (مانند فولاد، مس، آلومینیوم)، پلیمرها (مانند PVC، پلیاتیلن)، کامپوزیتها و سایر مواد مهندسی میشوند. پس از انتخاب ماده اولیه، آن را به ابعاد و شکلهای مورد نظر برش داده و آماده ورود به مراحل بعدی فرآیند تولید مینمایند. این مرحله، تأثیر مستقیمی بر کیفیت و عملکرد نهایی لوله خواهد داشت.
- فرآیند شکلدهی:
مرحله شکلدهی قلب تپنده تولید لولههای صنعتی است. در این مرحله، مواد اولیه آماده شده، با استفاده از روشهای مختلف و دقیق به شکل لولههای توخالی و استوانهای درمیآیند. بسته به نوع لوله و کاربرد آن، فرآیند شکلدهی میتواند شامل روشهای گوناگونی مانند اکستروژن، نورد، جوشکاری و خمکاری باشد. در روش اکستروژن، ماده اولیه از طریق یک قالب تحت فشار عبور کرده و شکل لوله را به خود میگیرد. در روش نورد، ورق فلزی به دور یک محور چرخان پیچیده شده و به شکل لوله در میآید. همچنین، در برخی موارد، از فرآیند جوشکاری برای اتصال دو لبه ورق فلزی و تشکیل لوله استفاده میشود. پس از شکلدهی اولیه، لولهها ممکن است نیاز به عملیات ثانویه مانند خمکاری، رزوهکاری یا سوراخکاری داشته باشند تا به شکل نهایی مورد نظر برسند. دقت در این مرحله بسیار مهم است، زیرا هرگونه خطا در شکلدهی میتواند بر عملکرد و کیفیت لوله تأثیر منفی بگذارد.
- تنظیمات فرآیند:
مرحله تنظیمات فرآیند در تولید لولههای صنعتی، گامی حیاتی برای تضمین کیفیت و یکپارچگی محصول نهایی است. در این مرحله، پارامترهای مختلفی از قبیل دما، فشار، سرعت تولید، ابعاد قالبها و تنظیمات دستگاهها با دقت بالایی تنظیم میشوند تا محصول تولیدی مطابق با استانداردهای تعیین شده باشد. هدف از این تنظیمات، بهینهسازی فرآیند تولید، کاهش ضایعات، افزایش دقت ابعادی لولهها و بهبود خواص مکانیکی آنها است. همچنین، کنترل دقیق فرآیند در این مرحله، موجب کاهش هزینههای تولید و افزایش راندمان خط تولید میشود. تنظیمات فرآیند معمولاً بر اساس نوع لوله، جنس مواد اولیه و مشخصات فنی محصول نهایی تعیین میشود و توسط متخصصان کنترل کیفیت به صورت دورهای بررسی و اصلاح میگردد.
- جوشکاری:
مرحله جوشکاری در تولید لولههای صنعتی، گامی کلیدی است که برای اتصال قطعات مختلف لوله و ایجاد یک ساختار یکپارچه و مقاوم انجام میشود. این فرایند معمولاً در تولید لولههای فلزی، به ویژه لولههای فولادی و آلیاژی، به کار میرود. پیش از شروع جوشکاری، آمادهسازی دقیق سطوح قطعات از اهمیت بالایی برخوردار است. این آمادهسازی شامل تمیزکاری کامل سطوح از هرگونه آلودگی، روغن، زنگزدگی و سایر ناخالصیها است تا اتصال جوش شده قوی و با دوام ایجاد شود. انتخاب روش جوشکاری مناسب نیز بر کیفیت و استحکام اتصال تأثیرگذار است. روشهای جوشکاری مختلفی مانند جوشکاری قوس الکتریکی، جوشکاری مقاومتی و جوشکاری لیزری در این صنعت مورد استفاده قرار میگیرند. هر یک از این روشها مزایا و کاربردهای خاص خود را دارند و انتخاب آنها به عوامل مختلفی همچون جنس ماده، ضخامت لوله و شرایط محیطی بستگی دارد.
- آزمون و کنترل کیفیت:
مرحله آزمون و کنترل کیفیت در تولید لولههای صنعتی، گامی حیاتی برای تضمین کیفیت و عملکرد مطلوب محصول نهایی است. در این مرحله، محصولات تولیدی تحت بررسیهای دقیق و همه جانبهای قرار میگیرند تا از تطابق آنها با استانداردهای تعیین شده و الزامات فنی پروژه اطمینان حاصل شود. آزمونهای مختلفی مانند آزمونهای مکانیکی (مقاومت کششی، فشار هیدرواستاتیک)، آزمونهای شیمیایی (آنالیز ترکیب شیمیایی)، آزمونهای فیزیکی (ضخامت سنجی، اندازه گیری ابعاد) و آزمونهای غیر مخرب (آزمون رادیوگرافی، آزمون التراسونیک) بر روی لولهها انجام میشود. هدف از این آزمونها، شناسایی هرگونه عیب یا نقص احتمالی در محصول، ارزیابی خواص مکانیکی و شیمیایی لولهها، و اطمینان از ایمنی و دوام آنها در شرایط کاری مختلف است. با انجام دقیق و مستمر این آزمونها، میتوان از تولید محصولات با کیفیت بالا و مطابق با استانداردهای بینالمللی اطمینان حاصل کرد.
- پوششدهی (اختیاری):
مرحله پوششدهی در تولید لولههای صنعتی، گامی مهم برای افزایش طول عمر و کارایی لولهها محسوب میشود. در این مرحله، با اعمال پوششهای محافظ مختلف بر روی سطح داخلی و خارجی لوله، مقاومت آن در برابر خوردگی، سایش، عوامل محیطی و مواد شیمیایی به طور قابل توجهی افزایش مییابد. انتخاب نوع پوشش به عواملی همچون جنس لوله، محیط کاری، نوع سیالی که در لوله جریان دارد و استانداردهای مورد نظر بستگی دارد. پوششهای رایج شامل پوششهای پلیمری (مانند پلیاتیلن، اپوکسی)، پوششهای فلزی (مانند گالوانیزه) و پوششهای ترکیبی هستند. این پوششها علاوه بر محافظت از لوله، به کاهش اصطکاک سیال با سطح داخلی لوله و جلوگیری از تشکیل رسوب نیز کمک میکنند. با انجام دقیق مرحله پوششدهی، لولههای تولیدی برای کاربرد در صنایع مختلف، از جمله نفت و گاز، آب و فاضلاب، صنایع شیمیایی و ساختمانی، آماده میشوند.
- آمادهسازی برای حمل و انبارداری:
مرحله آمادهسازی برای حمل و انبارداری در تولید لولههای صنعتی، گامی حیاتی برای حفظ کیفیت و یکپارچگی محصول تا رسیدن به مقصد نهایی است. در این مرحله، لولهها پس از گذراندن تمامی مراحل تولید، به دقت آمادهسازی شده و بستهبندی میشوند تا در طول حمل و نقل و انبارداری، از هرگونه آسیب فیزیکی، خوردگی یا آلودگی مصون بمانند. بستهبندی مناسب شامل استفاده از مواد بستهبندی با کیفیت، مانند ورقهای فلزی، پلاستیکهای محافظ یا پوششهای ضد زنگ، است تا از سطوح لوله محافظت شود. همچنین، لولهها به صورت منظم و با رعایت اصول ایمنی روی پالتها یا در بستهبندیهای مخصوص قرار گرفته و محکمبندی میشوند تا از جابجایی و برخورد آنها در حین حمل و نقل جلوگیری شود. علاوه بر این، اطلاعات فنی مربوط به لولهها مانند جنس، ابعاد، وزن و استانداردهای کیفی روی بستهبندی درج میشود تا شناسایی و ردیابی آنها به راحتی امکانپ پذیر باشد. با انجام دقیق این مرحله، اطمینان حاصل میشود که لولهها در شرایط مطلوب به دست مشتری رسیده و آماده نصب و استفاده شوند.
قیمت لوله های صنعتی
قیمت لولههای صنعتی تحت تاثیر عوامل متعددی قرار دارد که موجب نوسانات و تفاوت قابل توجه در قیمت انواع مختلف این محصولات میشود. جنس لوله، یکی از مهمترین عوامل تعیینکننده قیمت است. به عنوان مثال، لولههای استیل ضدزنگ به دلیل مقاومت بالا در برابر خوردگی و حرارت، قیمتی بالاتر از لولههای آهنی یا پلاستیکی دارند. قطر و ضخامت لوله نیز بر قیمت تاثیرگذار است؛ لولههای با قطر بزرگتر و ضخامت بیشتر معمولاً هزینه بیشتری دارند. علاوه بر این، عوامل بازار مانند عرضه و تقاضا، نوسانات قیمت مواد اولیه، هزینههای حمل و نقل و همچنین استانداردها و مشخصات فنی خاص هر لوله، بر قیمت نهایی آن موثر هستند. استفاده از پوششهای محافظ مانند گالوانیزه یا پوششهای مقاوم به خوردگی نیز به هزینه تولید میافزاید. همچنین، سفارشات با حجم بالا معمولاً شامل تخفیفات ویژهای میشوند. در نهایت، کاربرد لوله در صنایع مختلف نیز بر قیمت آن تاثیرگذار است؛ چرا که لولههایی که برای شرایط خاص مانند مقاومت در برابر حرارت بالا یا محیطهای خورنده تولید میشوند، دارای هزینههای تولید بیشتری هستند.
به طور خلاصه، قیمت لولههای صنعتی یک متغیر وابسته به عوامل متعدد است و نمیتوان قیمت ثابتی برای همه انواع لولهها در نظر گرفت. برای اطلاع دقیق از قیمت لوله صنعتی مورد نیاز خود، بهتر است با کارشناسان فروش بای آهن تماس گرفته و با ارائه مشخصات دقیق لوله مورد نظر، از قیمت روز آن مطلع شوید.
تفاوت لوله های صنعتی با گاز
لولههای صنعتی و لوله گازی، هر دو در سیستمهای لوله کشی کاربرد دارند، اما تفاوتهای اساسی در جنس، کاربرد، مقاومت و تنوع آنها وجود دارد. لولههای گاز به طور تخصصی برای انتقال گاز طبیعی یا مایعات نفتی طراحی شدهاند و معمولاً در شبکههای توزیع گاز شهری و صنعتی مورد استفاده قرار میگیرند. این لولهها معمولاً از جنس فولاد یا پلیاتیلن ساخته میشوند و به دلیل شرایط کاری خاص، مقاومت بالایی در برابر خوردگی دارند. در مقابل، لولههای صنعتی طیف وسیعی از مواد و آلیاژها را شامل میشوند و در صنایع مختلف مانند نفت، گاز، پتروشیمی، آب و فاضلاب و ساخت و ساز کاربرد دارند. این لولهها در اندازهها، ضخامتها و جنسهای متنوعی تولید میشوند تا بتوانند نیازهای مختلف صنایع را برآورده کنند.
یکی دیگر از تفاوتهای مهم این دو نوع لوله، تنوع در کاربرد آنها است. لولههای گاز معمولاً در سیستمهای توزیع با فشار نسبتا ثابت و در محیطهای مشخص استفاده میشوند، در حالی که لولههای صنعتی در شرایط کاری بسیار متنوعی از جمله دماهای بالا، فشارهای زیاد و محیطهای خورنده به کار میروند. به همین دلیل، لولههای صنعتی نیازمند مقاومت مکانیکی و شیمیایی بالاتری هستند. همچنین، از نظر اقتصادی، قیمت لولههای صنعتی به دلیل تنوع مواد و فرآیندهای تولید پیچیدهتر، معمولاً بالاتر از لولههای گاز است، به خصوص لولههای صنعتی با آلیاژهای خاص یا پوششهای مقاوم به خوردگی.
استانداردهای متنوع لولههای صنعتی
انتخاب استاندارد مناسب برای لولههای صنعتی، گامی حیاتی در تضمین کیفیت و عملکرد مطلوب آنها در صنایع مختلف است. تنوع بالای لولههای صنعتی، از نظر جنس، ابعاد و کاربرد، منجر به وجود استانداردهای متعدد برای آنها شده است.
- استاندارد ASTM: یکی از شناختهشدهترین و پرکاربردترین استانداردهای جهانی برای لولههای صنعتی است. استانداردهای ASTM A106، ASTM A192 و ASTM A179 نمونههایی از این استاندارد هستند.
- ASTM A106 : این استاندارد برای لولههای فولادی کربنی بدون درز طراحی شده است که برای کاربرد در دماهای بالا و فشارهای بالا مناسب هستند. این لولهها معمولاً در صنایع نفت و گاز مورد استفاده قرار میگیرند.
- ASTM A192 : لولههای مطابق با این استاندارد، به طور معمول برای ساخت دیگهای بخار به کار میروند و دارای خواص مکانیکی خاصی هستند تا در شرایط دمای بالا و فشار بخار مقاومت کنند.
- ASTM A179 : این استاندارد برای لولههای فولادی با درصد کربن پایینتر طراحی شده است و به دلیل انعطافپذیری بالا، اغلب در ساخت کندانسورها استفاده میشود.
- استاندارد GB 3087 : این استاندارد چینی، به طور ویژه برای لولههای مورد استفاده در بویلرها تدوین شده است و مشخصات فنی دقیق برای این نوع لولهها ارائه میدهد.
تنوع لولههای صنعتی و کاربردهای گسترده آنها
لولههای صنعتی به عنوان رگهای حیاتی صنایع مختلف، در اشکال، اندازهها و جنسهای متنوعی تولید میشوند. انتخاب مناسبترین نوع لوله، به عوامل متعددی از جمله نوع سیال منتقل شونده، فشار کاری، دمای محیط، شرایط خوردگی و بودجه پروژه بستگی دارد. در نتیجه، پاسخ به سوال "پرکاربردترین نوع لوله صنعتی کدام است؟" به سادگی امکانپذیر نیست.
- لولههای فولادی: به دلیل مقاومت بالا در برابر فشار، حرارت و سایش، لولههای فولادی به عنوان یکی از پرکاربردترین انواع لولههای صنعتی شناخته میشوند. این لولهها در صنایع نفت و گاز، پتروشیمی، ساخت و ساز و حمل و نقل کاربرد گستردهای دارند.
- لولههای فولادی گالوانیزه: با پوشش دهی فولاد با لایه روی، مقاومت این لولهها در برابر خوردگی به شدت افزایش مییابد. به همین دلیل، از آنها در سیستمهای آبیاری، ساخت و ساز و صنایع غذایی استفاده میشود.
- لولههای فولادی ضد زنگ: این لولهها به دلیل مقاومت بسیار بالا در برابر خوردگی، در صنایع غذایی، دارویی، شیمیایی و صنایع دریایی کاربرد دارند.
- لولههای آهنی: به دلیل قیمت مناسب و مقاومت قابل قبول در برابر فشار، لولههای آهنی در سیستمهای گرمایشی، شبکههای آب و گاز و ساخت و ساز مورد استفاده قرار میگیرند.
- لولههای تخصصی: علاوه بر لولههای فولادی و آهنی، لولههای تخصصی دیگری مانند لولههای چدنی، مسی، آلومینیومی و پلاستیکی نیز بسته به کاربرد خاص، مورد استفاده قرار میگیرند. برای مثال:
- لولههای چدنی: به دلیل مقاومت بالا در برابر خوردگی، در سیستمهای فاضلاب و شبکههای آب استفاده میشوند.
- لوله مسی: به دلیل هدایت حرارتی بالا، در سیستمهای سرمایشی و گرمایشی استفاده میشوند.
- لولههای پلاستیکی (PVC، پلی اتیلن): به دلیل وزن سبک، مقاومت در برابر خوردگی و سهولت نصب، در سیستمهای آبیاری، فاضلاب و گازرسانی استفاده میشوند.
انتخاب صحیح نوع لوله صنعتی، عاملی کلیدی در موفقیت پروژههای صنعتی است. با توجه به تنوع بالای لولههای صنعتی، مقایسه دقیق آنها بر اساس ویژگیهای مختلف، امری ضروری است. در این مقاله، به دو جنبه مهم در مقایسه لولههای صنعتی میپردازیم:
- کاربرد و استانداردها:
- تنوع کاربرد: لولههای صنعتی طیف گستردهای از کاربردها را پوشش میدهند، از انتقال سیالات داغ و خورنده در صنایع پتروشیمی تا انتقال آب و گاز در ساختمانها.
- استانداردهای مختلف: هر نوع لوله صنعتی باید با استانداردهای مشخصی مطابقت داشته باشد تا کیفیت و ایمنی آن تضمین شود. استانداردهایی مانند ASTM، DIN و ISO، الزامات فنی و ایمنی را برای انواع مختلف لولهها تعیین میکنند.
- اهمیت ایمنی: در کاربردهایی مانند انتقال گاز، رعایت استانداردهای ایمنی بسیار حیاتی است. لولههای مورد استفاده در این صنایع باید از مقاومت مکانیکی بالا و قابلیت اطمینان برخوردار باشند.
- جنس ورق و مقاومت مکانیکی:
- تنوع مواد: لولههای صنعتی از مواد مختلفی مانند فولاد، چدن، مس، آلومینیوم و پلاستیک تولید میشوند. هر یک از این مواد، ویژگیهای منحصر به فردی از جمله مقاومت در برابر خوردگی، حرارت، فشار و ضربه را دارا هستند.
- فولاد: فولاد به دلیل مقاومت بالا در برابر فشار و حرارت، در صنایع سنگین مانند نفت و گاز کاربرد فراوانی دارد.
- چدن: چدن به دلیل مقاومت در برابر خوردگی، در سیستمهای فاضلاب و شبکههای آب استفاده میشود.
- مس: مس به دلیل هدایت حرارتی بالا، در سیستمهای سرمایشی و گرمایشی کاربرد دارد.
- آلومینیوم: آلومینیوم به دلیل وزن سبک و مقاومت در برابر خوردگی، در صنایع هوافضا و ساختمان استفاده میشود.
- پلاستیک: پلاستیک به دلیل وزن سبک، مقاومت در برابر خوردگی و سهولت نصب، در سیستمهای آبیاری و فاضلاب استفاده میشود.
- عوامل موثر در انتخاب لوله:
علاوه بر جنس و کاربرد، عوامل دیگری نیز در انتخاب لوله صنعتی موثر هستند:
- فشار کاری: لوله باید بتواند فشار سیال را تحمل کند.
- دمای کاری: لوله باید در برابر تغییرات دمایی مقاوم باشد.
- محیط کاری: شرایط محیطی مانند رطوبت، خوردگی و ارتعاشات بر انتخاب لوله تاثیرگذار است.
- هزینه: قیمت لوله و هزینههای نصب و نگهداری نیز در تصمیمگیری موثر هستند.