پایپینگ، دنیایی از لولهها (بخش دوم)
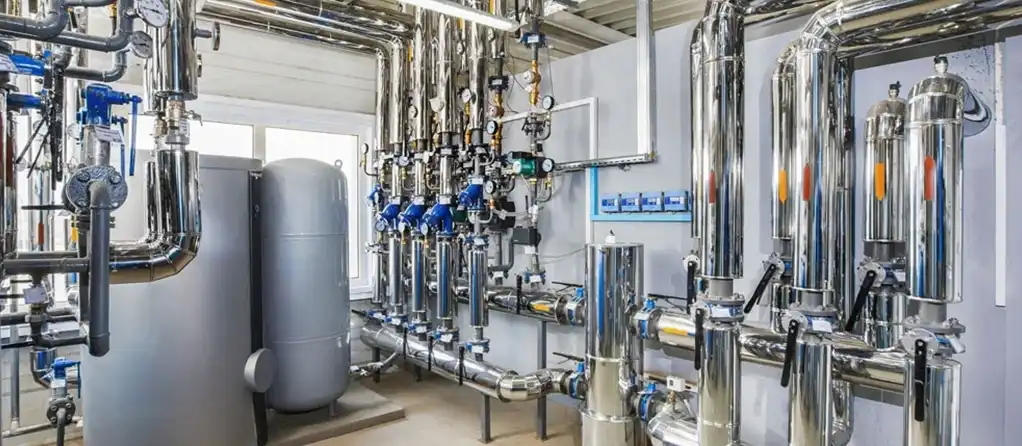
در لوله کشی صنعتی یا پایپینگ، انتخاب نوع لوله از اهمیت بالایی برخوردار است و به عوامل مختلفی از جمله کاربرد، شرایط محیطی و استانداردهای صنعتی بستگی دارد. برخلاف لوله کشی ساختمان که معمولاً از لولههای PVC برای انتقال آب و فاضلاب استفاده میشود، در صنایع مختلف از انواع متنوعی لوله با جنسهای مختلف بهره گرفته میشود.
برای مثال، در صنایع شیمیایی، نیروگاهها، پالایشگاهها و سیستمهای تهویه مطبوع، به دلیل شرایط کاری خاص و نیاز به مقاومت در برابر خوردگی، حرارت و فشار، از لولههایی با جنسهای خاصی مانند استیل، چدن، مس و آلومینیوم استفاده میشود. انتخاب جنس لوله در این صنایع بر اساس استانداردهای بینالمللی مانند ASME B31 انجام میشود که مشخصات فنی، نحوه نصب و ایمنی سیستمهای لولهکشی را تعریف میکند. این استانداردها تضمین میکنند که سیستمهای لولهکشی صنعتی با بالاترین کیفیت و ایمنی طراحی و اجرا شوند.
فولاد به عنوان یکی از پرکاربردترین مواد در صنایع مختلف، نقش محوری در سیستمهای لولهکشی صنعتی ایفا میکند. دو دسته اصلی لولههای فولادی عبارتند از:
- لولههای فولادی بدون درز: این نوع لولهها از یک قطعه فولادی یکپارچه ساخته میشوند و به همین دلیل استحکام و مقاومت بسیار بالایی دارند.
- لولههای فولادی درزدار: این لولهها از جوش دادن ورقهای فولادی به یکدیگر تولید میشوند و در مقایسه با لولههای بدون درز، معمولاً قیمت پایینتری دارند.
علاوه بر لولهها، از فولادهای فورج شده نیز به طور گسترده در ساخت اتصالات و قطعاتی که نیاز به استحکام و مقاومت بالایی دارند، استفاده میشود. فولادهای ریختهگری شده نیز در مواردی که شکل پیچیده و ابعاد بزرگ مورد نیاز باشد، به کار میروند.
فولادهای مورد استفاده در سیستمهای لولهکشی
با توجه به تنوع بالای فولادها، لازم است به بررسی دقیقتر انواع فولادهای مورد استفاده در سیستمهای لولهکشی بپردازیم. این فولادها بر اساس ترکیب شیمیایی، خواص مکانیکی و کاربردشان به دستههای مختلفی تقسیم میشوند که از جمله آنها میتوان به موارد زیر اشاره کرد:
- فولادهای کربنی: این فولادها به دلیل قیمت مناسب و خواص مکانیکی مناسب، در کاربردهای عمومی و انتقال سیالات با فشار و دما متوسط استفاده میشوند.
- فولادهای آلیاژی: با افزودن عناصر آلیاژی مانند کروم، نیکل و مولیبدن به فولادهای کربنی، خواصی مانند مقاومت به خوردگی، مقاومت به حرارت و استحکام را بهبود میبخشند.
- فولادهای زنگنزن: این فولادها حاوی حداقل 10.5 درصد کروم هستند و به دلیل مقاومت بسیار بالا در برابر خوردگی، در صنایع غذایی، دارویی و شیمیایی کاربرد گستردهای دارند.
- فولادهای مقاوم به حرارت: این فولادها قادر به تحمل دماهای بسیار بالا هستند و در صنایع متالورژی و نیروگاهی استفاده میشوند.
انتخاب نوع فولاد مناسب
انتخاب نوع فولاد مناسب برای یک سیستم لولهکشی، به عوامل مختلفی مانند نوع سیال، دما، فشار، محیط کاری و استانداردهای ایمنی بستگی دارد. مهندسان طراح با توجه به این عوامل و با استفاده از نرمافزارهای تخصصی، مناسبترین نوع فولاد را برای هر کاربرد انتخاب میکنند.
فولاد کربنی
فولاد کربنی به دلیل فراوانی، قیمت مناسب و خواص مکانیکی مناسب، به عنوان یکی از پرکاربردترین مواد در ساخت لولههای صنعتی شناخته میشود. این نوع فولاد حاوی مقادیر مختلفی کربن است که به طور مستقیم بر خواص مکانیکی و کاربرد آن تأثیر میگذارد.
طبقهبندی فولادهای کربنی بر اساس درصد کربن:
- فولادهای ملایم (Mild Steels): با درصد کربن کمتر از 0.3 درصد، این فولادها دارای قابلیت شکلدهی بالا و جوشکاری آسان هستند.
- فولادهای کربن متوسط (Medium Carbon Steels): با درصد کربن بین 0.3 تا 0.6 درصد، این فولادها استحکام و سختی بیشتری نسبت به فولادهای ملایم دارند.
- فولادهای با کربن بالا (High Carbon Steels): با درصد کربن بیش از 0.6 درصد، این فولادها بسیار سخت و مقاوم هستند اما شکلپذیری کمتری دارند.
تأثیر درصد کربن بر خواص مکانیکی:
افزایش درصد کربن در فولاد باعث افزایش استحکام و سختی آن میشود، اما در عین حال باعث کاهش شکلپذیری و جوشپذیری آن میشود. به عنوان مثال:
- فولادهایی با بیش از 0.35 درصد کربن تمایل به شکنندگی دارند.
- فولادهایی با بیش از 0.43 درصد کربن به سختی جوشکاری میشوند.
استانداردها و گریدهای فولاد کربنی:
استانداردهای ASTM A53 و ASTM A106 مشخصات فنی فولادهای کربنی مورد استفاده در لولههای صنعتی را تعیین میکنند. این استانداردها سه گرید اصلی A، B و C را تعریف میکنند که هر کدام استحکام کششی متفاوتی دارند.
- گرید A: کمترین استحکام کششی را دارد و معمولاً برای کاربردهای عمومی استفاده میشود.
- گرید B: استحکام کششی بیشتری نسبت به گرید A دارد و حاوی کربن و منگنز بیشتری است.
- گرید C: بالاترین استحکام کششی را دارد و برای کاربردهایی که نیاز به استحکام بالا دارند مانند لولههای تحت فشار استفاده میشود.
فولادهای آلیاژی
فولادهای آلیاژی با افزودن عناصر آلیاژی مختلف به فولاد کربن، خواصی مانند استحکام، سختی، مقاومت به خوردگی و حرارت را بهبود میبخشند. هر عنصر آلیاژی تأثیر خاصی بر خواص فولاد دارد و به همین دلیل، فولادهای آلیاژی طیف گستردهای از کاربردها را در صنایع مختلف پیدا کردهاند. در ادامه به بررسی برخی از مهمترین انواع فولادهای آلیاژی میپردازیم:
- فولادهای نیکلدار: نیکل چقرمگی فولاد را افزایش داده و مقاومت آن را در برابر دماهای پایین بهبود میبخشد. این فولادها در صنایع هوافضا و نفت و گاز کاربرد فراوانی دارند.
برای اطلاع از قیمت لوله نفت با کارشناسان فروش بای آهن تماس حاصل نمایید.
- فولادهای مولیبدندار: مولیبدن به فولاد استحکام و مقاومت به سایش میدهد و اغلب در ترکیب با کروم و نیکل استفاده میشود. این فولادها در ساخت ابزارهای برش و قطعات خودرو کاربرد دارند.
- فولادهای کرومدار: کروم مقاومت فولاد را در برابر خوردگی و اکسیداسیون افزایش میدهد. فولادهای زنگنزن که حاوی حداقل 10.5 درصد کروم هستند، نمونهای از این نوع فولادها هستند.
- فولادهای کروم-وانادیومدار: این فولادها ترکیبی از استحکام بالا و وزن کم دارند و در ساخت قطعات خودرو و سازههای هواپیما کاربرد دارند.
- فولادهای تنگستندار: تنگستن سختی فولاد را در دماهای بالا حفظ میکند و در ساخت ابزارهای برش و قطعات موتور استفاده میشود.
- فولادهای منگنزدار: منگنز استحکام و سختی فولاد را افزایش میدهد و در ساخت قطعاتی که در معرض سایش هستند، مانند ریلهای راه آهن، کاربرد دارد.
برای اطلاع از قیمت لوله آلیاژی با کارشناسان بای آهن تماس بگیرید.
فولاد زنگ نزن (استنلس استیل)
فولاد زنگ نزن، آلیاژی از آهن است که با افزودن حداقل 12 درصد کروم، مقاومت بسیار بالایی در برابر خوردگی و اکسیداسیون پیدا میکند. این ویژگی منحصربهفرد، فولاد زنگ نزن را به یکی از پرکاربردترین مواد در صنایع مختلف تبدیل کرده است. علاوه بر کروم، عناصری مانند نیکل، مولیبدن، تیتانیوم و سایر عناصر آلیاژی نیز به فولاد زنگ نزن اضافه میشوند تا خواص آن را بهبود بخشیده و طیف گستردهای از گریدهای فولاد زنگ نزن با ویژگیهای متفاوت ایجاد کنند.
لولههای ساخته شده از فولاد زنگ نزن به دلیل مزایای فراوانی که دارند، در صنایع مختلف کاربرد گستردهای پیدا کردهاند. از جمله این مزایا میتوان به مقاومت در برابر خوردگی و اکسیداسیون، مقاومت در برابر دماهای بالا، حفظ خلوص مواد در تماس با لوله و هزینههای نگهداری پایین اشاره کرد. این ویژگیها باعث شده است که لولههای فولاد زنگ نزن در صنایع غذایی، شیمیایی، دارویی، نفت و گاز و بسیاری از صنایع دیگر مورد استفاده قرار گیرند.
فولادهای زنگ نزن توسط موسسه آهن و فولاد آمریکا (AISI) به دو دسته اصلی سری 200-300 و سری 400 تقسیمبندی میشوند. هر یک از این سریها شامل گریدهای مختلفی است که هر کدام خواص و کاربردهای خاص خود را دارند.
فولادهای زنگ نزن آستنیتی
فولادهای زنگ نزن آستنیتی، به ویژه سری 300، پرکاربردترین نوع فولاد زنگ نزن هستند. این فولادها به دلیل ساختار کریستالی آستنیتی خود، از قابلیت شکلپذیری بالا، جوشکاری آسان و مقاومت خوب در برابر خوردگی برخوردار هستند.
گریدهای رایج فولاد آستنیتی:
- گرید 304: این گرید با ترکیب 18 درصد کروم و 8 درصد نیکل، یکی از رایجترین و اقتصادیترین گریدهای فولاد زنگ نزن است. گرید 304 به دلیل مقاومت خوب در برابر خوردگی و شکلپذیری بالا، در صنایع غذایی، شیمیایی و ساختمانی کاربرد گستردهای دارد. با این حال، در دماهای بالا (400 تا 900 درجه سانتیگراد) مستعد خوردگی بیندانهای است.
- گرید 304L: این گرید مشابه گرید 304 است، اما با محتوای کربن بسیار پایینتر. کاهش محتوای کربن باعث میشود که این گرید در برابر خوردگی بیندانهای مقاومتر باشد و در کاربردهایی که نیاز به جوشکاری مکرر دارند، مناسبتر باشد.
- گرید 316: این گرید حاوی مولیبدن اضافی است که مقاومت آن را در برابر خوردگی، به ویژه در محیطهای کلریدی، به طور قابل توجهی افزایش میدهد. گرید 316 در صنایع شیمیایی، دریایی و پزشکی کاربرد دارد.
استانداردهای تولید لولههای فولاد زنگ نزن:
- ASTM A312: این استاندارد برای لولههای فولاد زنگ نزن با قطر کمتر از 8 اینچ استفاده میشود.
- ASTM A358: این استاندارد برای لولههای فولاد زنگ نزن با قطر 8 اینچ و بالاتر استفاده میشود.
- ASTM A409: این استاندارد برای لولههای فولاد زنگ نزن با ضخامت دیواره نازک استفاده میشود.
فولادهای زنگ نزن سری 400
فولادهای زنگ نزن سری 400 به دو دسته اصلی فریتی و مارتنزیتی تقسیم میشوند. این فولادها معمولاً حاوی کروم بیشتری نسبت به فولادهای آستنیتی هستند و در نتیجه مقاومت به خوردگی آنها نیز بیشتر است. با این حال، قابلیت شکلپذیری و جوشکاری آنها کمتر از فولادهای آستنیتی است.
فولاد فریتی
فولادهای فریتی، زیرمجموعهای از فولادهای زنگ نزن هستند که به دلیل ساختار کریستالی خاص خود، ویژگیهای متمایزی دارند. این فولادها حاوی 12 تا 18 درصد کروم و مقدار کمی کربن (0.08 تا 0.2 درصد) هستند.
ویژگیهای اصلی فولادهای فریتی:
- مقاومت به خوردگی: فولادهای فریتی مقاومت خوبی در برابر خوردگی جوی و برخی محیطهای خورنده دارند، اما مقاومت آنها به اندازه فولادهای آستنیتی نیست.
- مغناطیسی بودن: بر خلاف بسیاری از فولادهای زنگ نزن دیگر، فولادهای فریتی خاصیت مغناطیسی دارند.
- جوشپذیری و شکلپذیری محدود: جوشکاری این فولادها به دلیل احتمال ایجاد ترکهای ناشی از تنش، نیازمند دقت و کنترل بیشتری است. شکلپذیری آنها نیز نسبت به فولادهای آستنیتی کمتر است.
- قیمت مناسب: به دلیل ساختار سادهتر و مواد اولیه ارزانتر، فولادهای فریتی معمولاً قیمت پایینتری نسبت به فولادهای آستنیتی دارند.
فولاد مارتنزیتی
فولاد مارتنزیتی، نوعی فولاد زنگنزن است که به دلیل ساختار کریستالی خاص خود، ویژگیهای منحصر به فردی دارد. این فولادها حاوی 12 تا 18 درصد کروم و مقدار قابل توجهی کربن (0.1 تا 1.2 درصد) هستند. همین ترکیب شیمیایی باعث شده است که فولادهای مارتنزیتی استحکام و سختی بسیار بالایی داشته باشند.
ویژگیهای اصلی فولادهای مارتنزیتی:
- استحکام بالا: فولادهای مارتنزیتی از بالاترین استحکام کششی در بین انواع فولاد زنگ نزن برخوردارند.
- سختی بالا: این فولادها به دلیل ساختار کریستالی مارتنزیتی، بسیار سخت هستند و مقاومت سایشی بالایی دارند.
- قابلیت عملیات حرارتی: فولادهای مارتنزیتی را میتوان با عملیات حرارتی سختکاری و تمپر کرد تا خواص مکانیکی آنها بهبود یابد.
- مغناطیسی بودن: برخلاف بسیاری از فولادهای زنگ نزن دیگر، فولادهای مارتنزیتی خاصیت مغناطیسی دارند.
- مقاومت خوردگی متوسط: مقاومت خوردگی این فولادها نسبت به فولادهای آستنیتی کمتر است، اما در بسیاری از کاربردها، مقاومت خوردگی آنها کافی است.
- جوشپذیری محدود: جوشکاری این فولادها به دلیل احتمال ایجاد ترکهای ناشی از تنش، نیازمند دقت و کنترل بیشتری است.
گرید 410، پرکاربردترین فولاد مارتنزیتی
گرید 410 یکی از رایجترین و شناختهشدهترین فولادهای مارتنزیتی است. این گرید به دلیل ترکیب مناسب از استحکام، سختی و مقاومت به خوردگی، در صنایع مختلفی از جمله ساخت ابزارآلات، قطعات خودرو و پرههای توربین استفاده میشود.
لوله های گالوانیزه
لوله گالوانیزه، در واقع یک لوله فولادی یا آهنی است که سطح داخلی و خارجی آن با لایه نازکی از فلز روی پوشیده شده است. این فرایند را گالوانیزاسیون مینامند. هدف از گالوانیزاسیون، افزایش مقاومت لوله در برابر خوردگی و زنگزدگی است. چرا که فلز روی، به دلیل واکنشپذیری بالاتر از آهن، به جای آهن با اکسیژن و رطوبت موجود در محیط واکنش میدهد و بدین ترتیب از خوردگی آهن زیرین جلوگیری میکند.
ویژگیهای لوله گالوانیزه:
- مقاومت بالا در برابر خوردگی: مهمترین ویژگی لوله گالوانیزه، مقاومت بالای آن در برابر زنگزدگی و خوردگی است. این ویژگی باعث میشود که لوله گالوانیزه عمر مفید طولانیتری نسبت به لولههای فولادی بدون پوشش داشته باشد.
- انعطافپذیری: لولههای گالوانیزه تا حدودی انعطافپذیر هستند و میتوان آنها را خم کرد.
- مقاومت مکانیکی خوب: لولههای گالوانیزه استحکام مکانیکی خوبی دارند و میتوانند فشارهای داخلی را تحمل کنند.
- نصب آسان: این لولهها به راحتی برش خورده و به یکدیگر متصل میشوند.
- قیمت مناسب: نسبت به برخی از لولههای دیگر، قیمت لوله گالوانیزه مناسبتر است.
سیستمهای پایپینگ به عنوان رگهای حیاتی صنایع مختلف عمل میکنند و نقش محوری در انتقال سیالات، گازها و مواد شیمیایی ایفا میکنند. این سیستمها به ویژه در صنایع نفت، گاز، پتروشیمی و فرآیندی که با محیطهای با فشار بالا و دمای شدید سروکار دارند، از اهمیت بالایی برخوردار هستند. لولهها و اتصالات به کار رفته در پایپینگ باید به گونهای طراحی شوند که در برابر خوردگی، سایش و فشارهای وارده مقاومت کنند. انتخاب صحیح متریال و طراحی دقیق، نقش کلیدی در اطمینان از عملکرد ایمن و بهینه این سیستمها دارد.
پایپینگ نه تنها به انتقال ساده سیالات میپردازد، بلکه به کنترل جریان، تنظیم فشار و دما و همچنین جلوگیری از نشت و آلودگی کمک میکند. طراحی و اجرای صحیح سیستمهای پایپینگ، به طور مستقیم بر بهرهوری و ایمنی فرآیندهای صنعتی تأثیر میگذارد. کاهش هزینههای عملیاتی، افزایش طول عمر تجهیزات و کاهش ریسک حوادث از جمله مزایای استفاده از سیستمهای پایپینگ بهینه هستند. علاوه بر این، پایپینگ نقش مهمی در حفاظت از محیط زیست ایفا میکند، زیرا از نشت مواد خطرناک به محیط زیست جلوگیری میکند.